Customizable high quality aluminum alloy battery box sheet metal casing | Youlian
Battery Box Product pictures
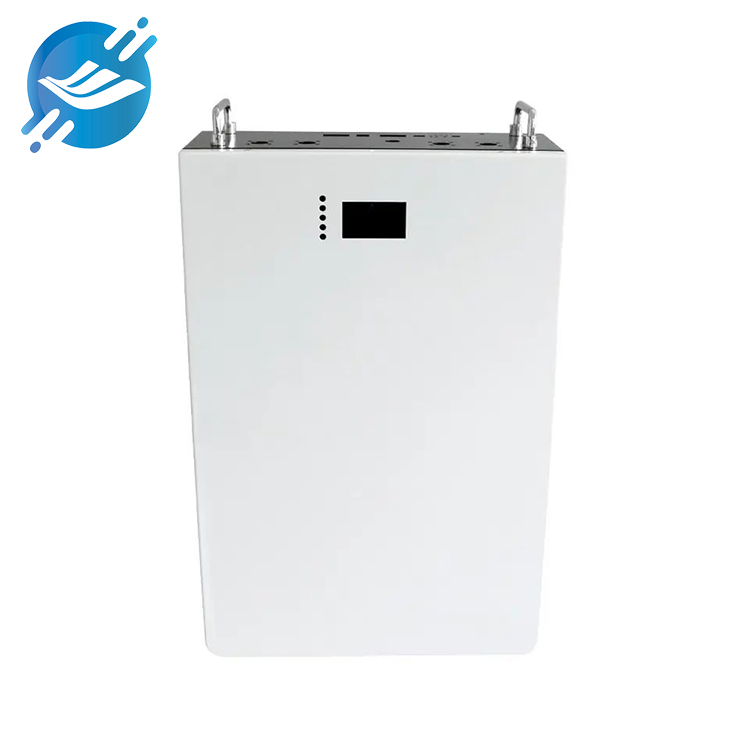
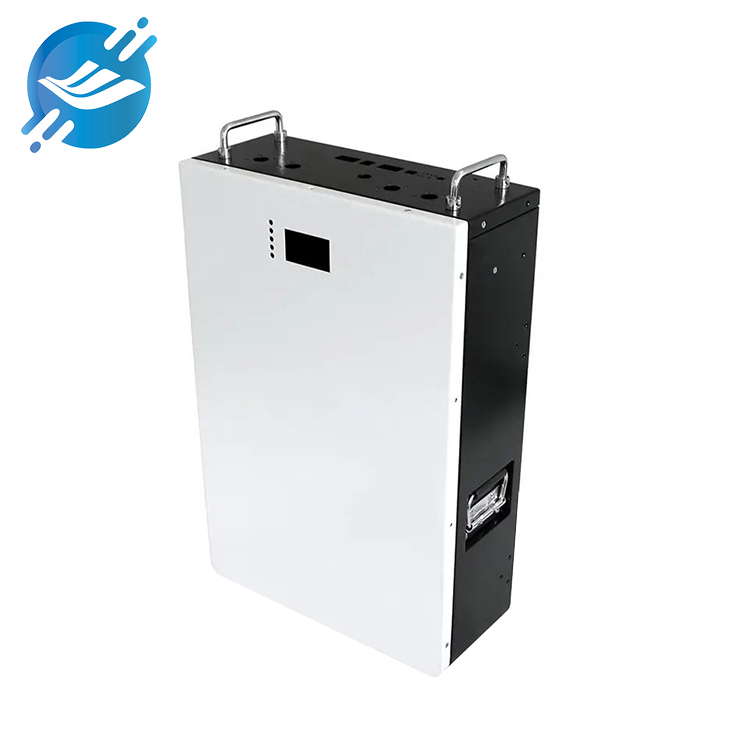
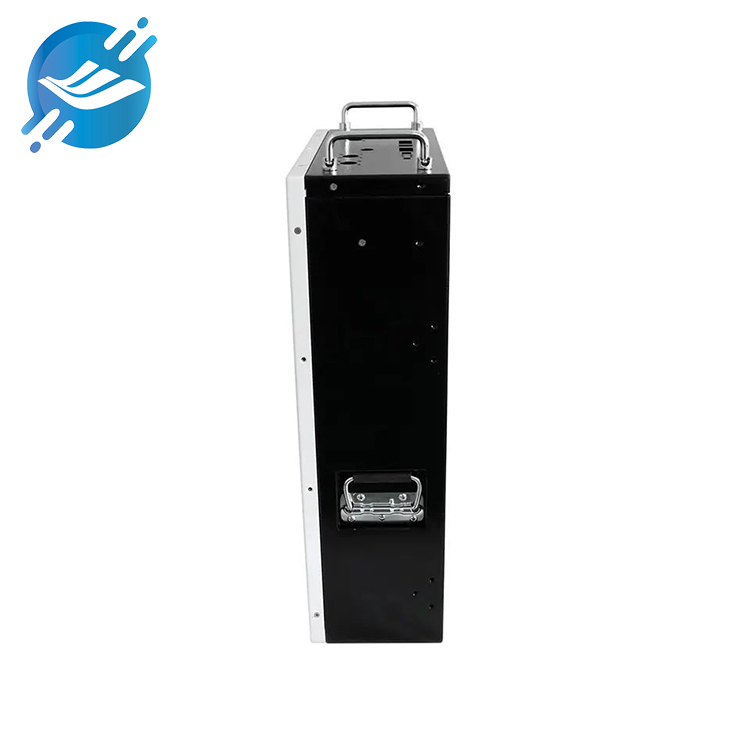
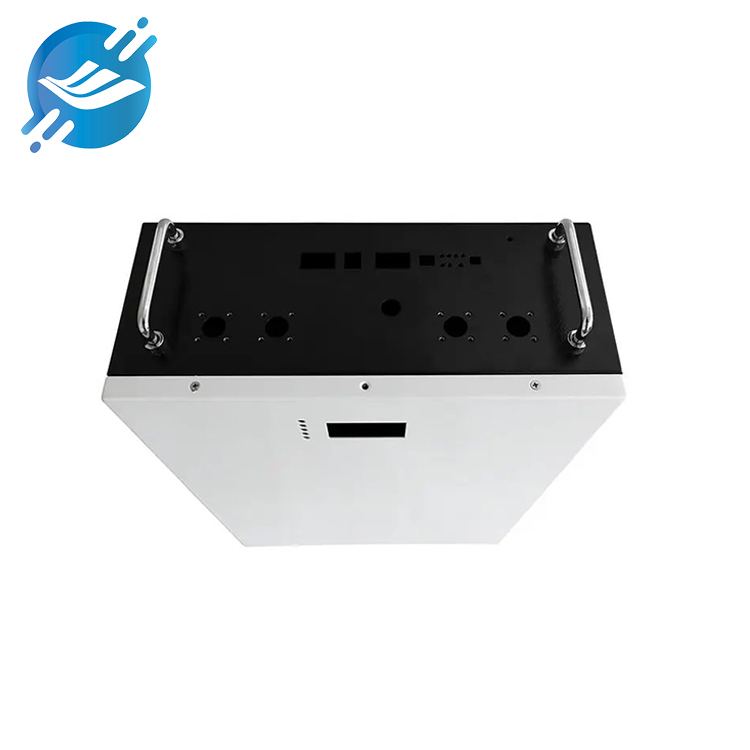
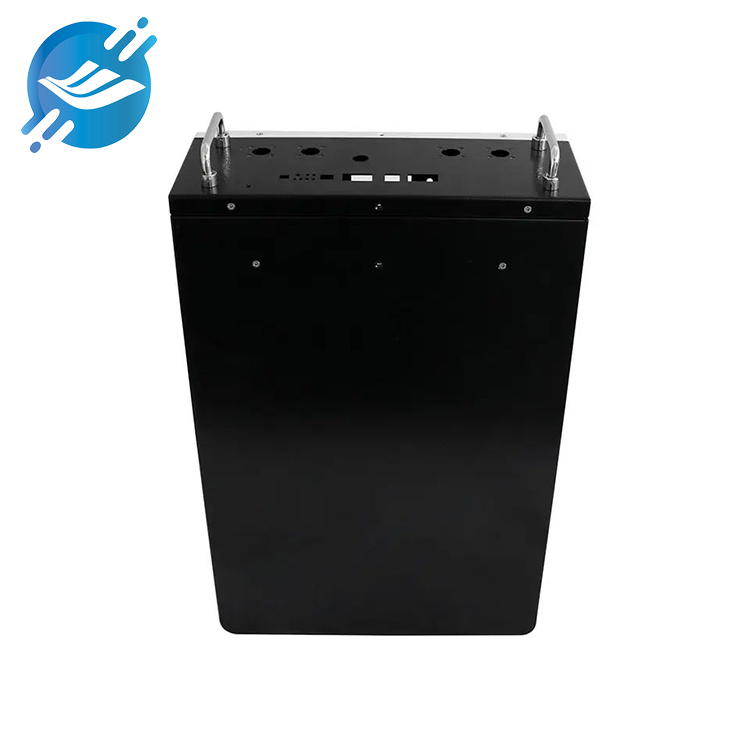
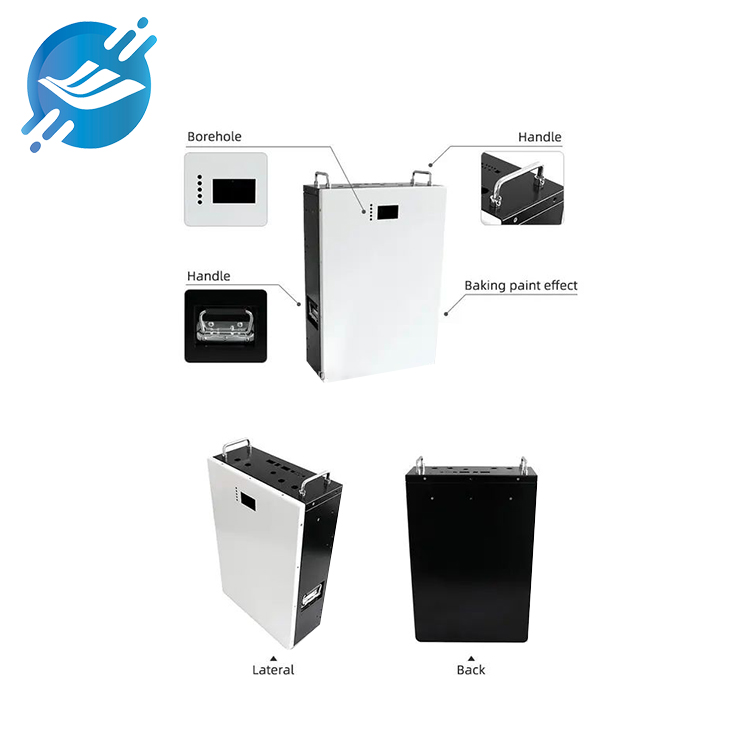
Battery Box Product parameters
Product name: | Customizable high quality aluminum alloy battery box sheet metal casing | Youlian |
Model Number: | YL1000062 |
Material: | The material of this Battery case is mainly iron/aluminum/stainless steel, etc. For example, automobile power battery aluminum shells and battery covers are mainly made of 3003 aluminum plates. The main alloying element is manganese, which is easy to process and form, has high temperature corrosion resistance, good heat transfer and electrical conductivity. |
Thickness: | The thickness of most power battery pack boxes is 5mm, which is less than 1% of the box thickness and has little impact on the mechanical properties of the box. If Q235 steel is used, the thickness is about 3.8 -4mm, using composite material T300/5208, the thickness is 6.0.mm |
Size: | 380*160*480MM OR Customized |
MOQ: | 100PCS |
Color: | The overall color is white and black or Customized |
OEM/ODM | Welocme |
Surface Treatment: | Laser, bending, grinding, powder coating, spray painting, galvanizing, electroplating, anodizing, polishing, nickel plating, chrome plating, grinding, phosphating, etc. |
Design: | Professional designers design |
Process: | Laser cutting,CNC bending, Welding,Powder coating |
Product Type | Battery case |
Battery Box Product Features
1.3003 aluminum alloy material has low density and soft material. It has the advantages of being easy to stretch and form the aluminum shell of power battery as a whole. It has been used by many companies for battery packaging.
2.The box body is made of aluminum alloy or stainless steel, with good strength, good hardness, beautiful surface, good sealing, good lifespan and easy maintenance.
3.Have ISO9001/ISO14001 certification
4.The battery box is mainly used to carry battery system components such as battery modules and cooling systems to protect the battery from damage when it is impacted and squeezed by the outside world.
5.No need for frequent repairs and replacements, saving maintenance costs and time.
6.The material of the external aluminum shell is mostly aluminum-manganese alloy, which has high strength, strong corrosion resistance, and can be heat treated, which greatly improves the service life of the lithium battery shell.
7.Protection level: IP54/IP55/IP65
8.The shape is changeable, it can be rectangular, round, square, triangle, etc. Any shape can be customized. Cylindrical lithium batteries use a mature winding process with a high degree of automation, stable product quality, and relatively low cost.
9.The casings of square hard-shell batteries are mostly made of aluminum alloy, stainless steel and other materials. The interior adopts winding or laminated technology, and the protection effect on the battery core is better than that of aluminum-plastic film batteries (i.e. soft-pack batteries).
10.Light weight, excellent processing performance, and good molding performance; excellent strength and stiffness, high impact resistance, and high safety performance; good corrosion resistance, impact resistance, stamping resistance, and stretchability, and not easy to break; energy saving Emission reduction, recycling and reuse are of high value.
Battery Box Product structure
Upper cover: The upper cover is the top covering part of the battery box, usually made of sheet metal material. It provides protection and sealing for the battery, and often has appropriate openings for wire connections and ventilation.
Base Plate: The base plate is the bottom portion of the battery box and is usually made of sheet metal material. It provides support and stability to the battery. Baseboards also usually have appropriate openings for electrical wiring and ventilation.
Four side walls: The four side walls of the battery box connect the upper cover and bottom plate to form a complete structure. These side walls are typically welded or bolted from a single or multiple pieces of sheet metal material. The geometry of the side walls can vary according to the design requirements of the battery box, such as rectangular, square or other shapes.
Reinforced support structure: In order to increase the rigidity and stability of the entire battery box, additional reinforced support structures are sometimes installed on the side walls. These support structures may be beams, stiffeners, or other profiles used to increase the overall strength of the battery box.
Connecting parts: In order to facilitate the installation and fixation of the battery box, connecting parts, such as bolts, nuts, rivets, etc., are usually installed between the upper cover, side walls, and bottom plates. These connecting parts can make the assembly of the battery box stronger and more reliable.
In general, the sheet metal structure of the battery box shell mainly includes the upper cover, bottom plate, side walls, reinforced support structure and connecting parts. These components work together to provide protection and support for the battery. The specific structure and construction may vary based on different battery box designs and requirements.
Workshop production process
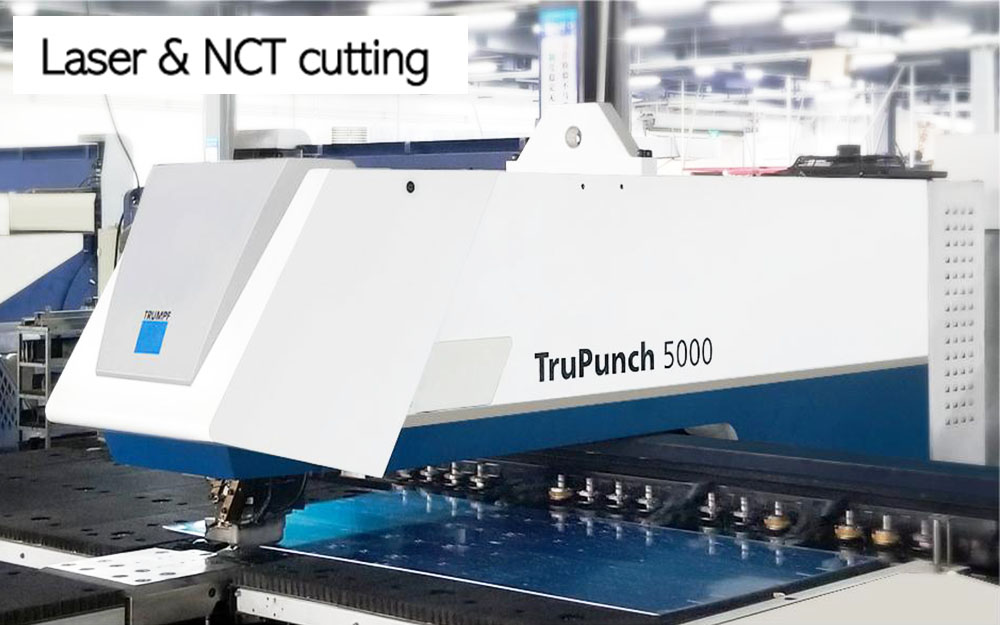
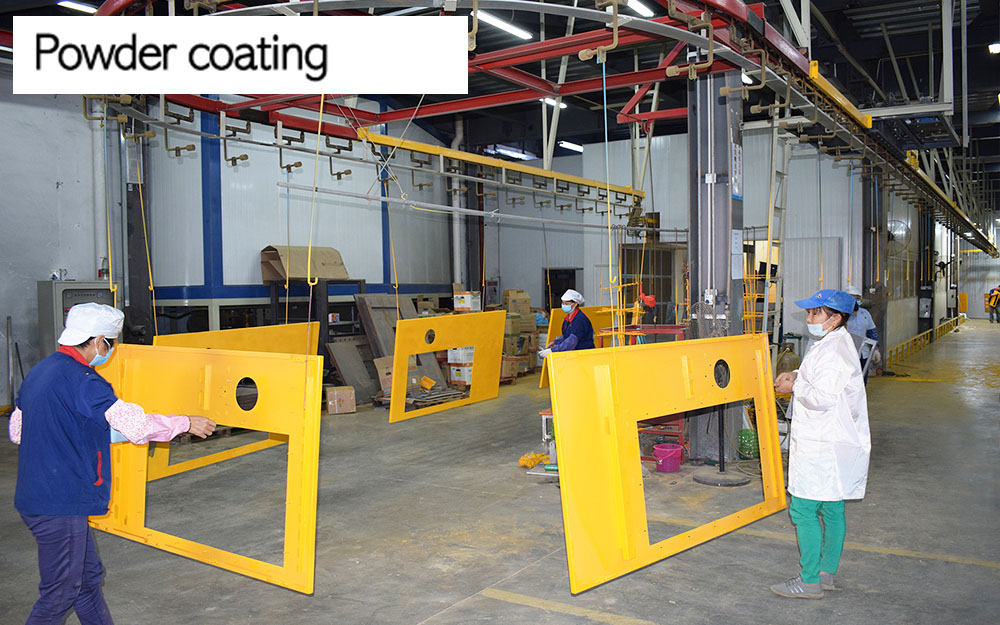
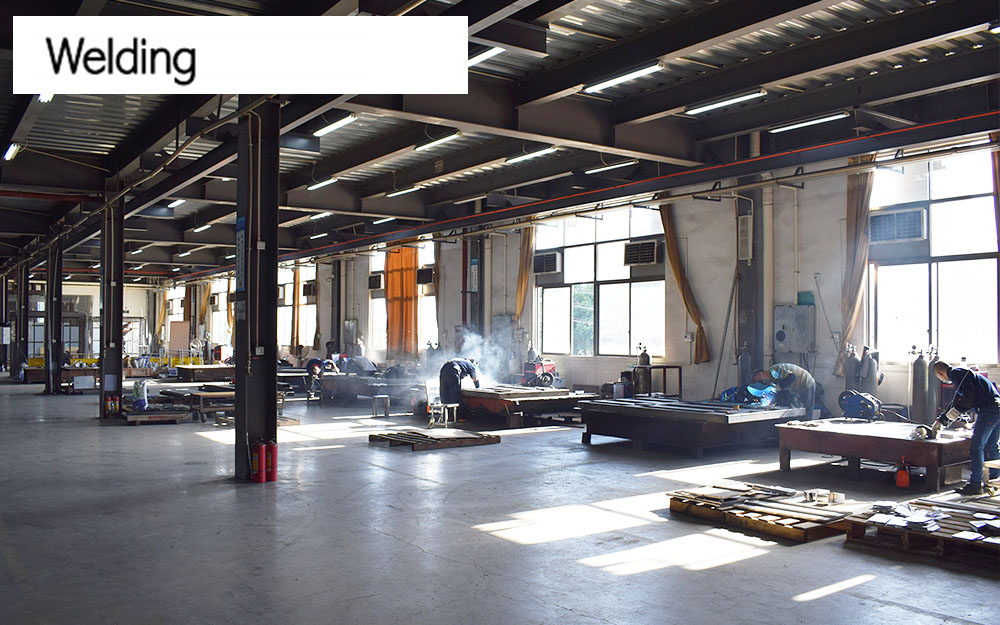
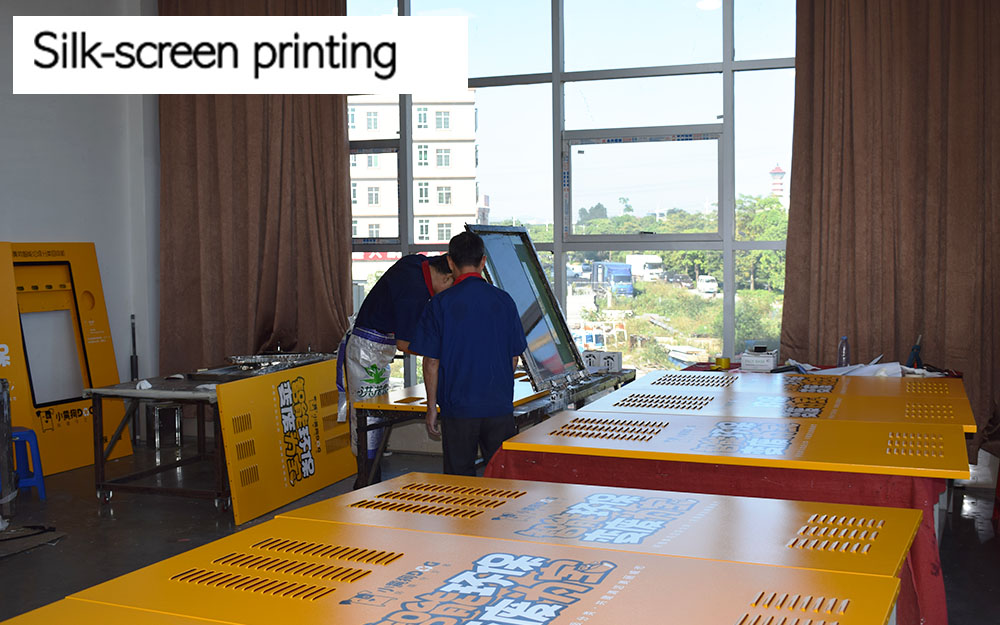
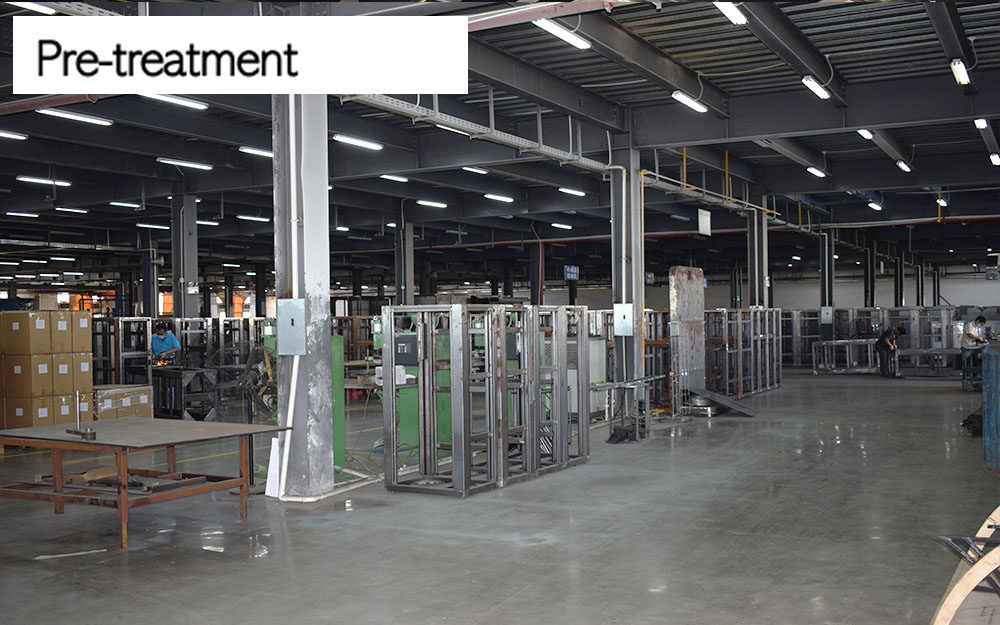

Factory strength
Dongguan Youlian Display Technology Co., Ltd. is a factory covering an area of more than 30,000 square meters, with a production scale of 8,000 sets/month. We have more than 100 professional and technical personnel who can provide design drawings and accept ODM/OEM customization services. The production time for samples is 7 days, and for bulk goods it takes 35 days, depending on the order quantity. We have a strict quality management system and strictly control every production link. Our factory is located at No. 15 Chitian East Road, Baishigang Village, Changping Town, Dongguan City, Guangdong Province, China.
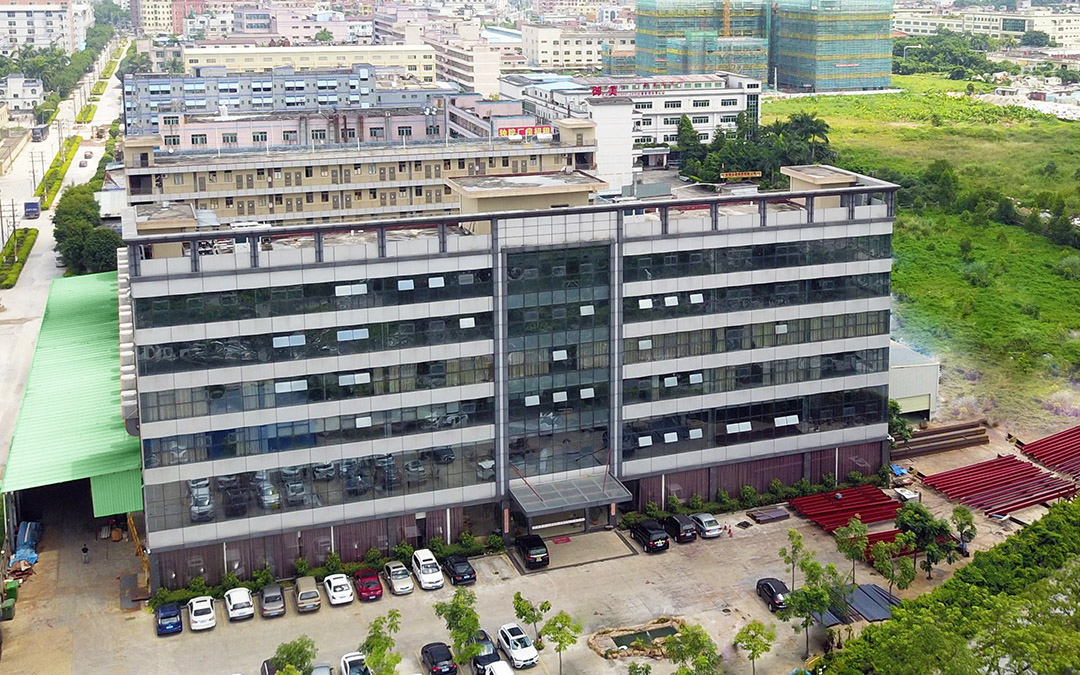
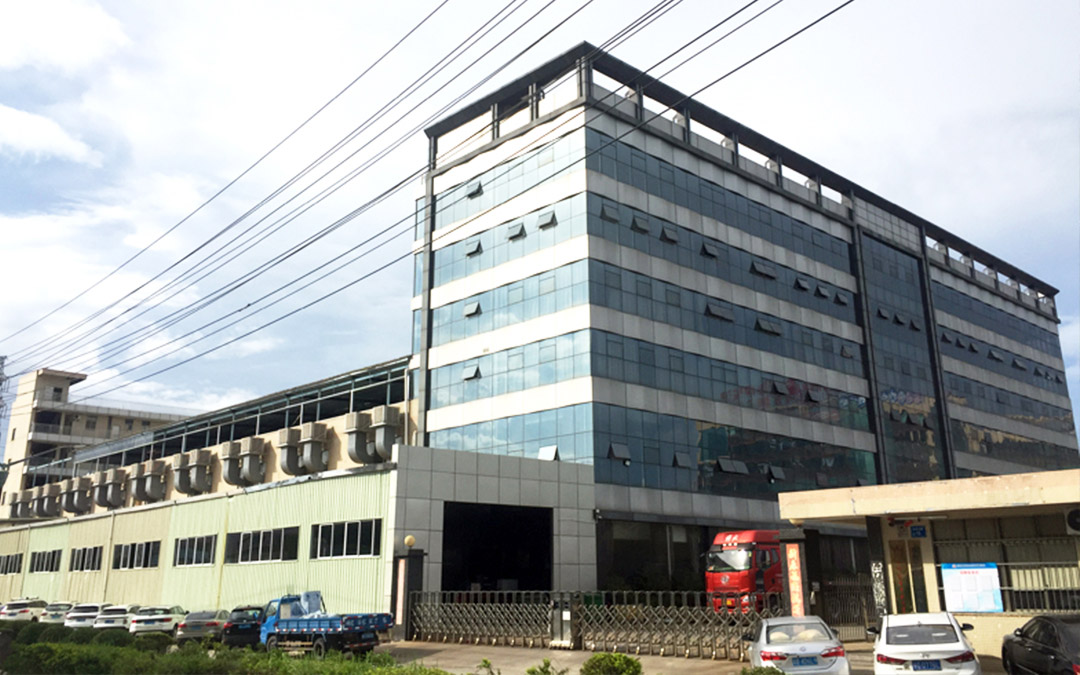
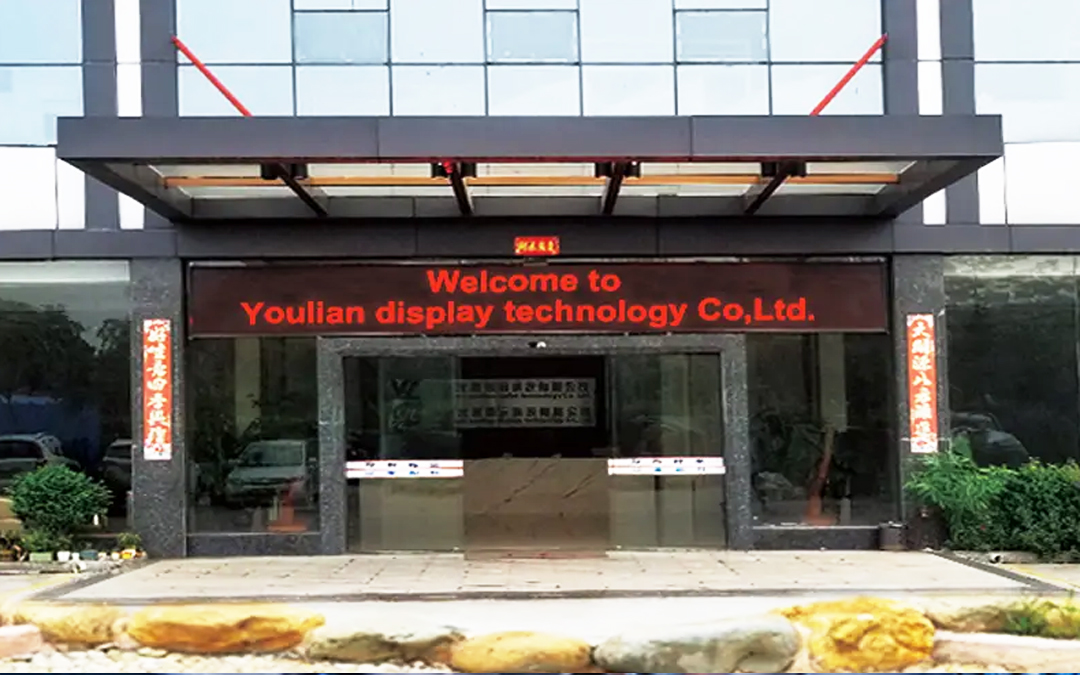
Mechanical Equipment
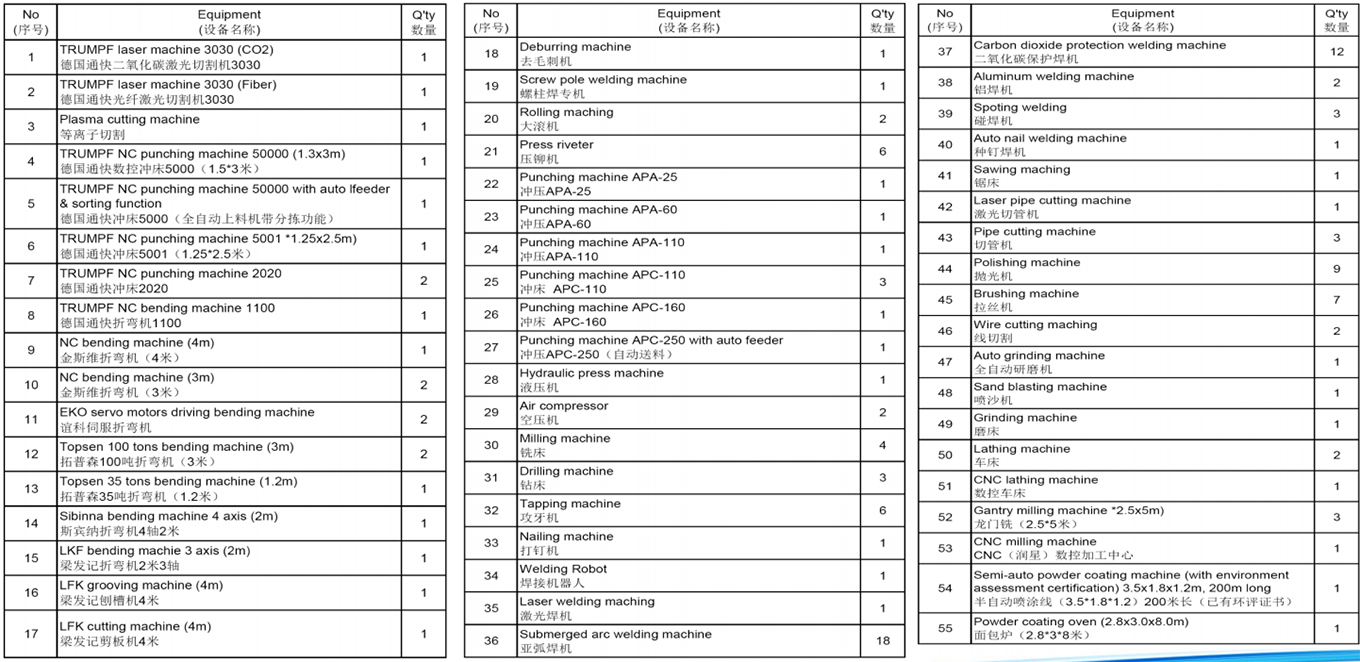
Certificate
We are proud to have achieved ISO9001/14001/45001 international quality and environmental management and occupational health and safety system certification. Our company has been recognized as a national quality service credence AAA enterprise and has been awarded the title of trustworthy enterprise, quality and integrity enterprise, and more.
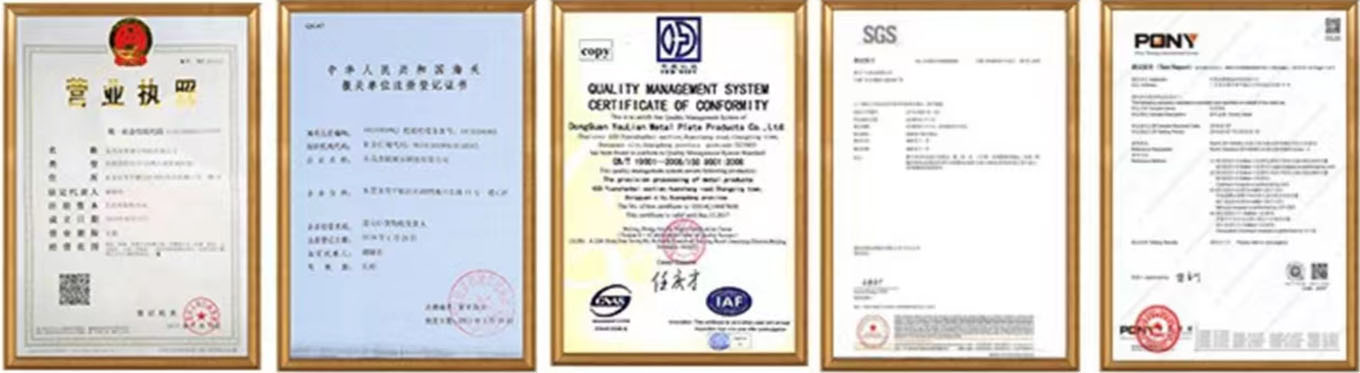
Transaction details
We offer various trade terms to accommodate different customer requirements. These include EXW (Ex Works), FOB (Free On Board), CFR (Cost and Freight), and CIF (Cost, Insurance, and Freight). Our preferred payment method is a 40% downpayment, with the balance paid before shipment. Please note that if an order amount is less than $10,000 (EXW price, excluding shipping fee), the bank charges must be covered by your company. Our packaging consists of plastic bags with pearl-cotton protection, packed in cartons and sealed with adhesive tape. Delivery time for samples is approximately 7 days, while bulk orders may take up to 35 days, depending on the quantity. Our designated port is ShenZhen. For customization, we offer silk screen printing for your logo. Settlement currency can be either USD or CNY.
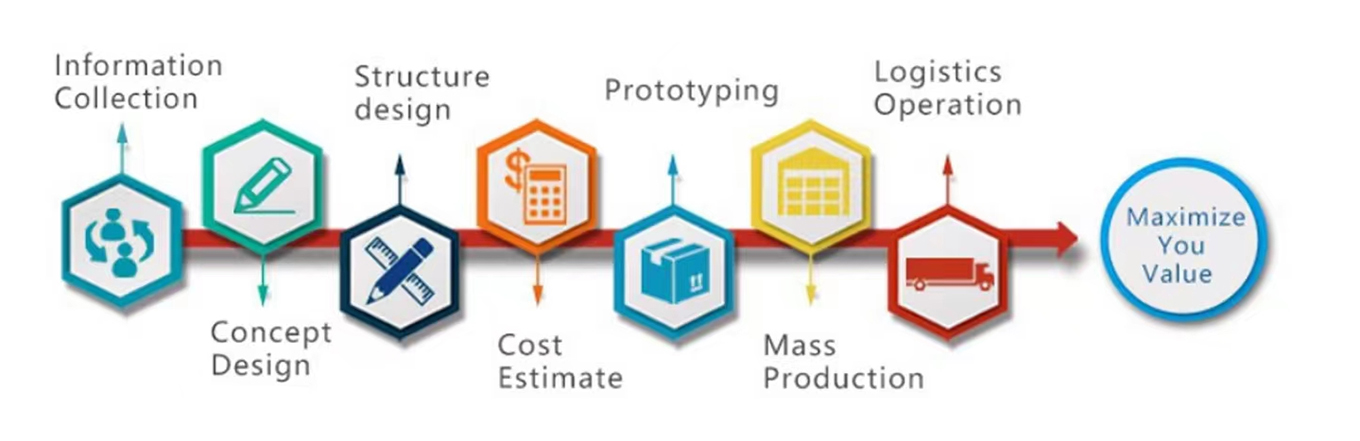
Distribution map of cooperative customers
Mainly distributed in European and American countries, such as the United States, Germany, Canada, France, the United Kingdom, Chile and other countries have our customer groups.
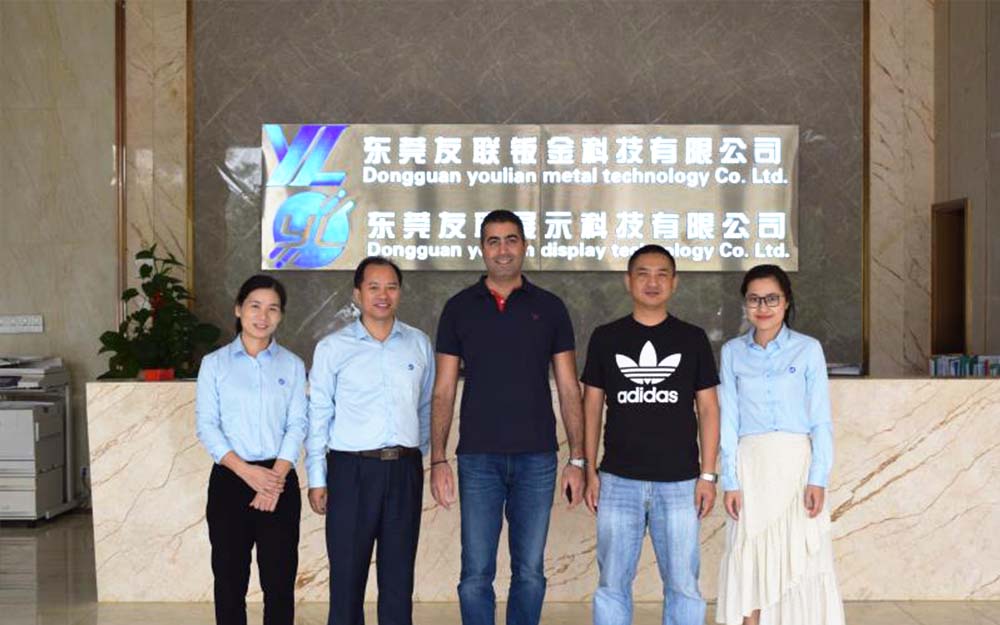
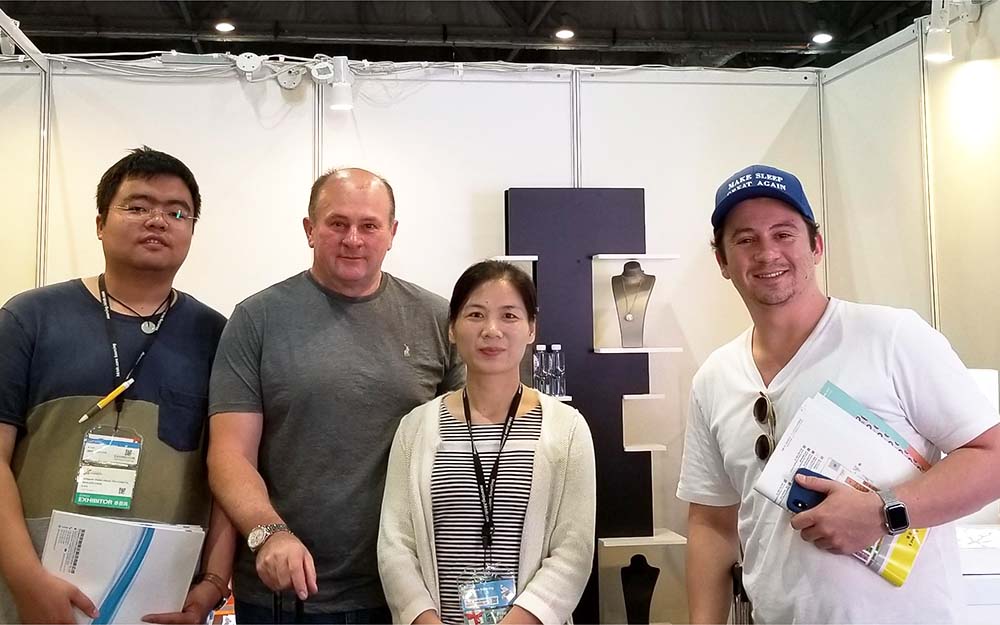
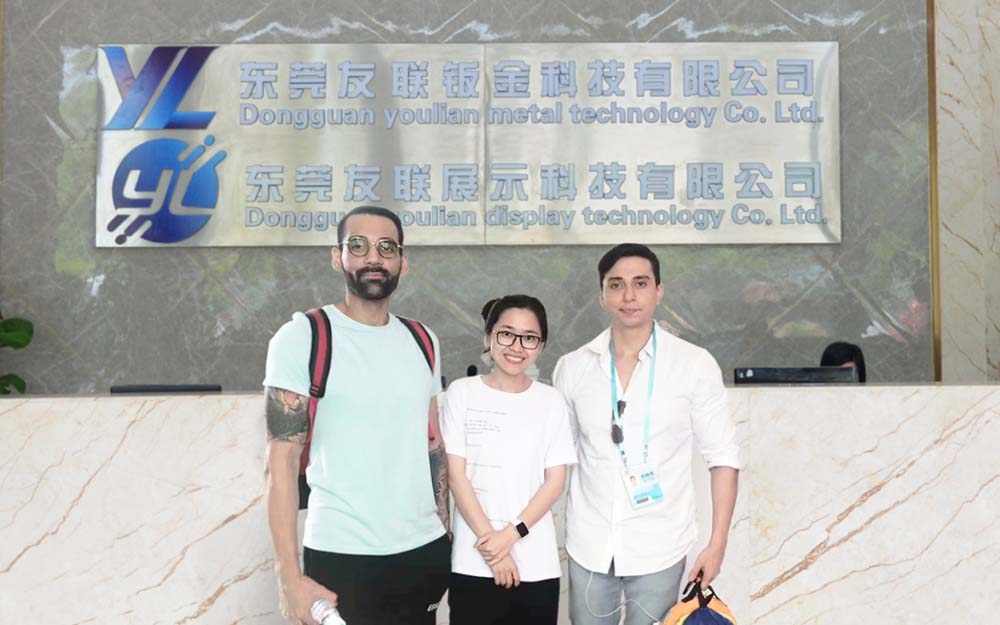
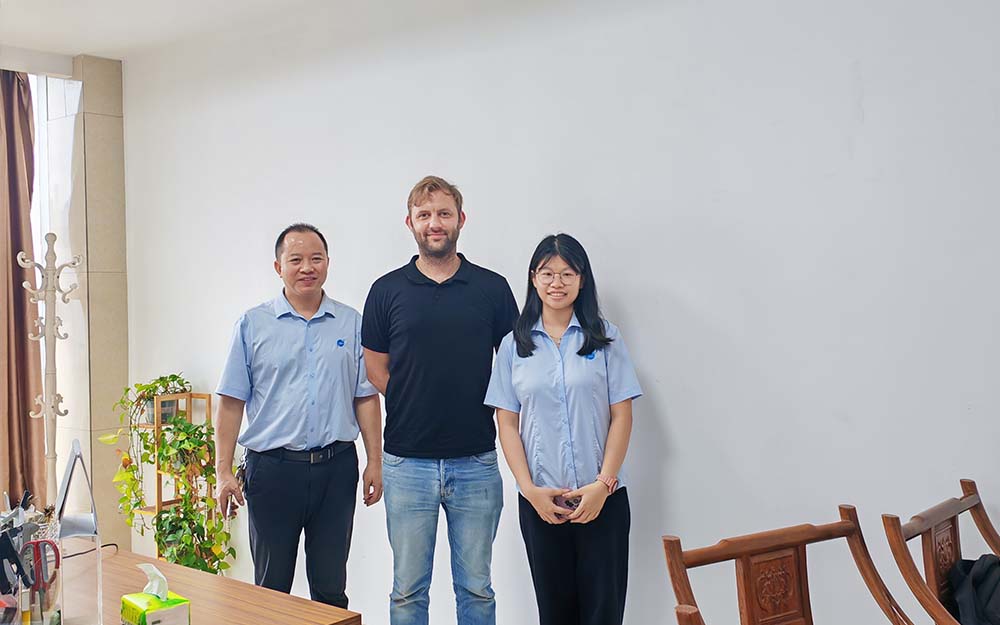
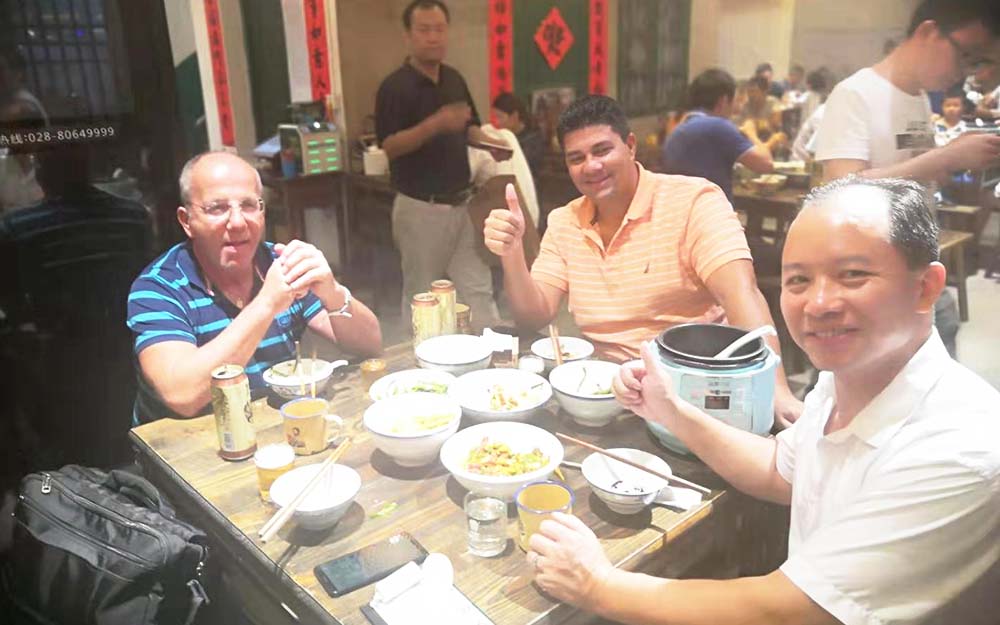
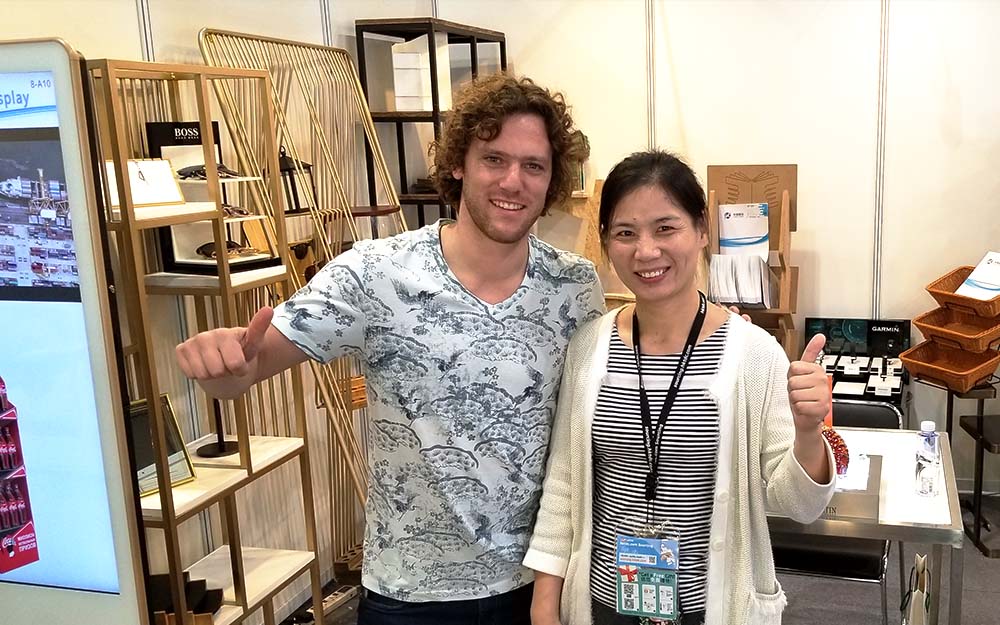
Our Team
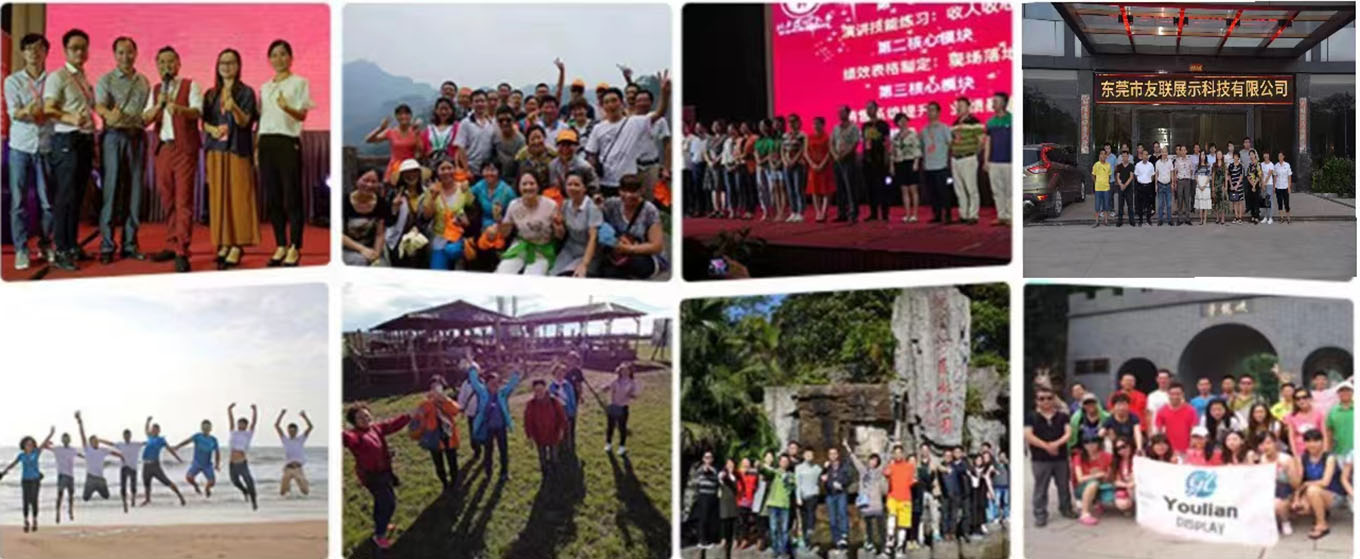