Biaya bagian pemrosesan lembaran logam terutama berasal dari tiga aspek: bahan baku, stamping dies dan biaya modal manusia.
Di antara mereka, bahan baku dan stamping die biaya bertanggung jawab atas proporsi utama, dan pabrik pembuatan dan pemrosesan logam lembaran perlu memulai dari kedua aspek ini untuk mengurangi biaya.
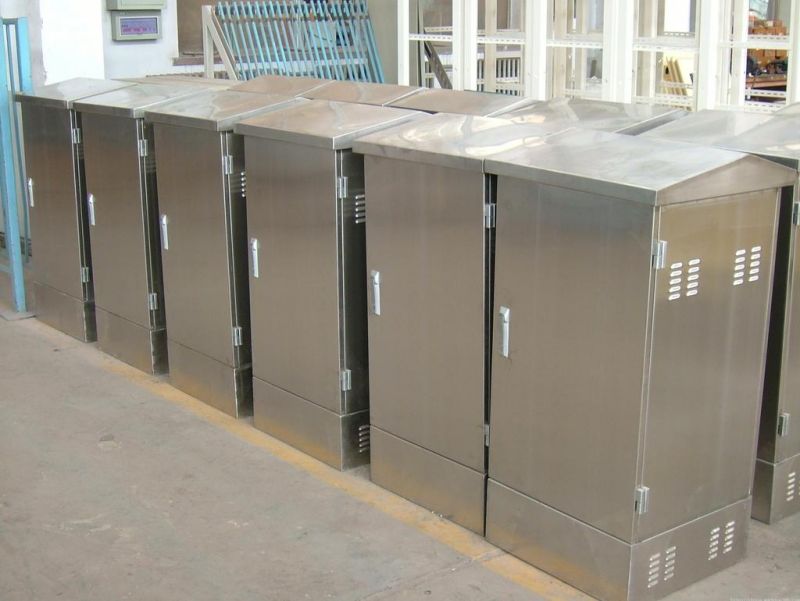
1. Seperti apa bagian lembaran logam itu
Bentuklembaran logamBagian harus kondusif untuk tata letak, meminimalkan limbah, dan meningkatkan pemanfaatan bahan baku. Desain bentuk lembaran logam yang efektif dapat mempromosikan pemanfaatan bahan baku yang tinggi dan lebih sedikit limbah selama tata letak lembaran logam, sehingga mengurangi biaya bahan baku logam lembaran. Kiat perbaikan minor tentang desain penampilan lembaran logam dapat sangat meningkatkan tingkat pemanfaatan bahan baku, sehingga menghemat biaya suku cadang.
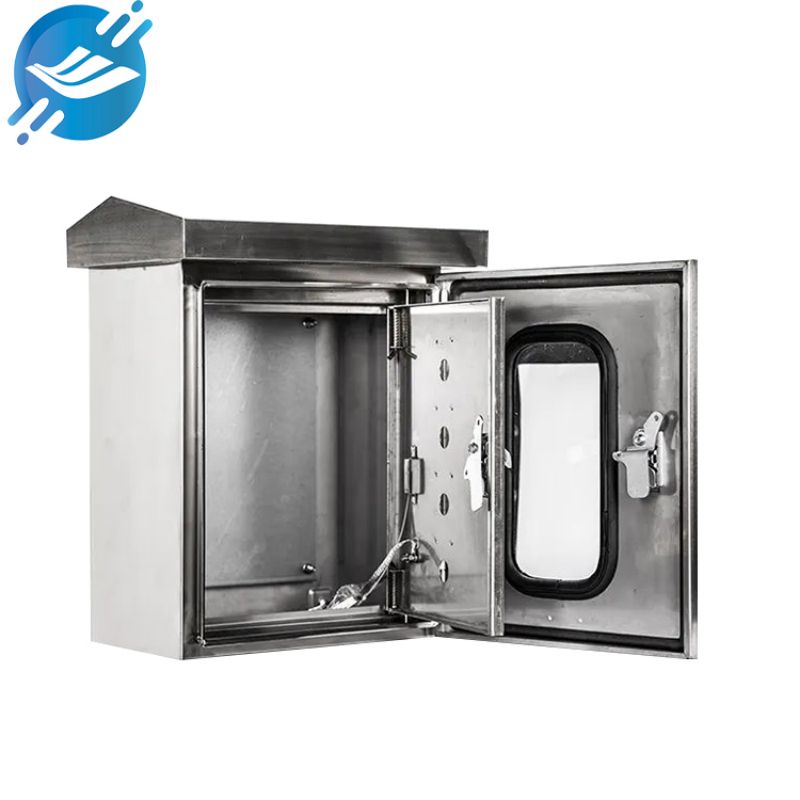
2. Kurangi ukuran lembaran logam
Lembaran logamUkuran adalah salah satu faktor penting yang menentukan biaya cetakan stamping logam lembaran. Semakin besar ukuran lembaran logam, semakin besar spesifikasi cetakan stamping, dan semakin tinggi biaya cetakan. Ini menjadi semakin jelas ketika cetakan stamping mencakup beberapa set cetakan proses stamping.
1) Hindari fitur panjang dan sempit pada lembaran logam. Bentuk logam lembaran sempit dan panjang tidak hanya memiliki kekerasan bagian -bagian yang rendah, tetapi juga mengkonsumsi bahan baku berat selama tata letak logam lembaran. Pada saat yang sama, fitur logam lembaran panjang dan sempit meningkatkan peningkatan spesifikasi cap die dan meningkatkan biaya cetakan.
2) Cegah lembaran logam dari penampilan berbentuk "sepuluh" setelah selesai. Lembaran logam dengan desain penampilan berbentuk "sepuluh" setelah selesai akan mengkonsumsi lebih banyak bahan baku selama tata letak. Pada saat yang sama, tingkatkan spesifikasi cetakan stamping dan tingkatkan biaya cetakan. .
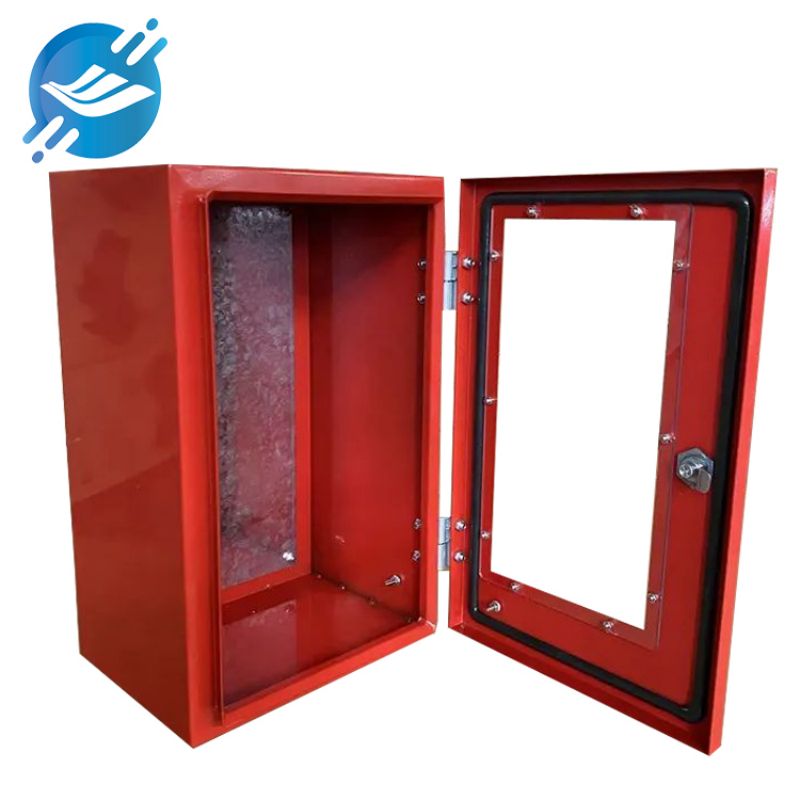
3. Buat desain penampilan lembaran logam sesederhana mungkin
Desain penampilan lembaran logam yang kompleks membutuhkan cetakan cekung dan rongga yang kompleks, yang meningkatkan biaya produksi cetakan dan pemrosesan. Desain penampilan lembaran logam harus sesederhana mungkin.
4. Kurangi jumlah proses mati stamping
Ada dua jenis utama cetakan stamping: cetakan rekayasa dan cetakan kontinu.Proyek lembaran logamCetakan kemungkinan akan mencakup beberapa set cetakan proses, seperti cetakan utama, cetakan lentur logam lembaran, membentuk cetakan, dan cetakan deburring. Semakin besar jumlah proses cetakan, semakin banyak proses yang akan ada untuk cetakan logam lembaran, dan semakin tinggi biaya cetakan stamping. Hal yang sama berlaku untuk mode kontinu. Biaya cetakan secara positif terkait dengan jumlah proses cetakan. Oleh karena itu, untuk mengurangi biaya cetakan cetakan, jumlah proses cetakan harus diminimalkan.
A. Tentukan tepi perekat secara efektif dari lentur lembaran logam. Tepi perekat yang tidak masuk akal dari lentur lembaran logam dapat dengan mudah memperlambat proses lentur logam lembaran.
B. Produk desain harus meminimalkan lentur logam lembaran yang berlebihan.
C. Produk desain harus meminimalkan lipat dan paving.
D. Selain itu, deburring umumnya membutuhkan proses deburring yang terpisah mati.
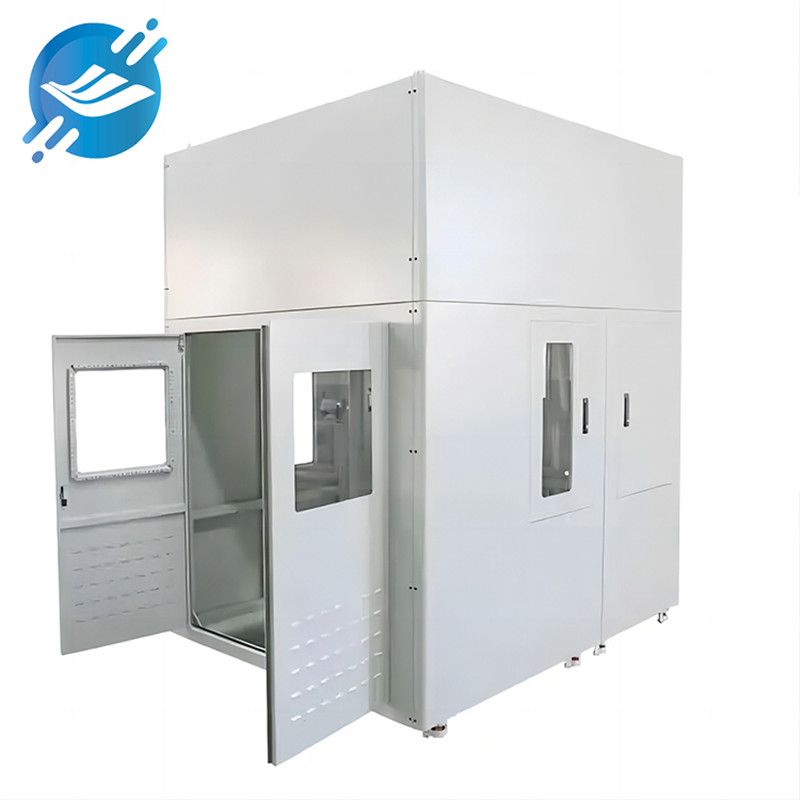
5. Secara efektif memilih metode pemasangan bagian:
Kunci ≤ paku keling ≤ mengacaukan diri ≤ pengelasan ≤ sekrup biasa ≤ sekrup yang mengencangkan tangan
6. Atur secara wajar struktur lembaran logam untuk mengurangi jumlah total bagian
Meskipun proses pembuatan stamping tidak memungkinkan bagian -bagian lembaran logam memiliki struktur yang kompleks, dalam lingkup bagian lembaran logam dapat diselesaikan, struktur bagian logam lembaran harus diatur secara wajar dan bagian perifer dari bagian logam lembaran harus digabungkan untuk mengurangi jumlah total bagian dan dengan demikian mengurangi biaya produk.
Waktu pos: Oktober-24-2023