섀시 캐비닛의 제조 및 생산에는 많은 주요 링크가 있습니다. 다음은 중요한 링크 중 일부입니다.
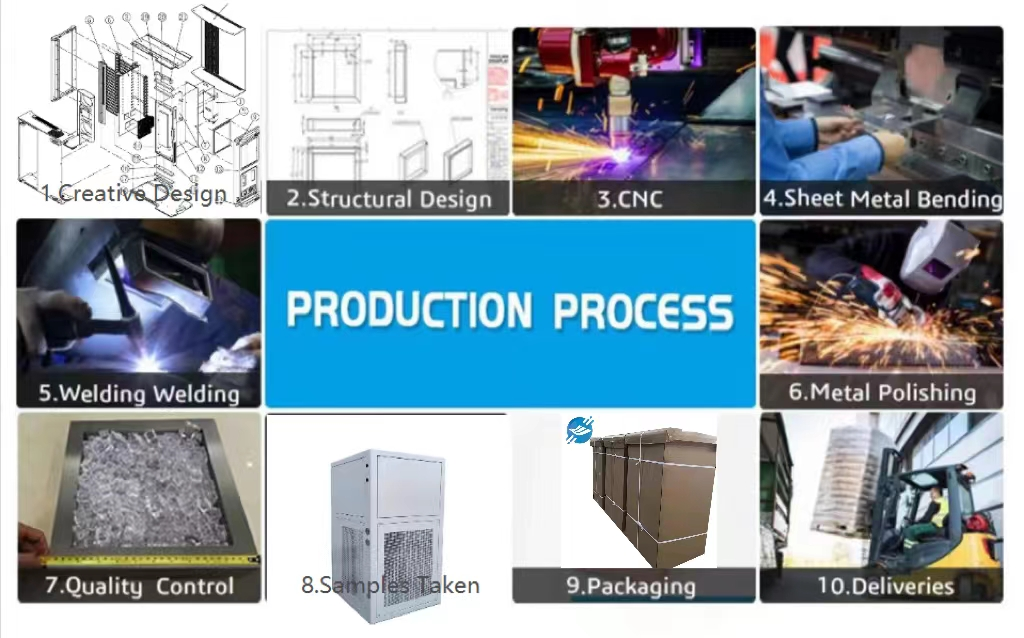
설계 및 R & D : 섀시 캐비닛의 설계 및 R & D는 전체 생산 공정의 단계입니다. 제품 구조 설계, 재료 선택, 외관 설계, 기능 레이아웃 등이 포함되며 제품 품질 및 성능과 관련이 있습니다.
재료 조달 : 섀시 및 캐비닛의 제조에는 냉간 압연 강판, 스테인레스 스틸 플레이트, 알루미늄 합금 등과 같은 대량의 금속 재료가 필요합니다. 이러한 재료의 품질은 섀시 및 캐비닛의 강도, 내구성 및 모양에 직접적인 영향을 미칩니다. 따라서 올바른 공급 업체를 선택하고 고품질 원자재를 구매하는 것이 매우 중요합니다.
재료 가공 : 구매 한 원료 가공은 섀시 캐비닛 생산에서 중요한 링크 중 하나입니다. 재료 절단, 펀칭, 굽힘, 용접 및 기타 공정이 포함됩니다. 이러한 프로세스에는 CNC 절단 기계, 굽힘 기계, 용접 기계 등과 같은 다양한 장비 및 도구를 사용해야합니다.
표면 처리 : 섀시와 캐비닛의 외관 품질은 소비자 만족도에 큰 영향을 미칩니다. 따라서 섀시와 캐비닛의 표면 처리는 매우 중요한 링크입니다. 일반적인 표면 처리 방법에는 분무, 플라스틱 분무, 전기 영동 코팅 등이 포함됩니다. 이러한 방법은 섀시 및 캐비닛의 외관 및 질감을 향상시키고 어느 정도의 부식 저항을 제공 할 수 있습니다.
어셈블리 및 테스트 : 섀시 및 캐비닛의 생산 단계에서 각 구성 요소를 조립하고 테스트해야합니다. 조립 프로세스는 섀시와 캐비닛의 구조가 안정적이고 기계적 조정이 양호되도록 설계 요구 사항에 따라 엄격하게 수행해야합니다. 테스트 프로세스에는 섀시 및 캐비닛의 기능 테스트, 전기 성능 테스트, 온도 테스트 등이 포함되어 제품이 제대로 작동하고 고객 요구를 충족시킬 수 있도록합니다.
품질 검사 및 품질 관리 : 전자 제품의 중요한 구성 요소로서 품질과 성능의 안정성은 전체 시스템의 안정적인 작동에 중요한 역할을합니다. 따라서 생산 공정에서 품질 검사 및 품질 관리가 필수적입니다. 품질 검사는 샘플링 검사, 테스트 장비, 테스트 프로세스 및 기타 수단을 통해 제품의 품질을 모니터링하여 제품이 설계 요구 사항 및 관련 표준을 충족 할 수 있도록 할 수 있습니다.
포장 및 배송 : 섀시 및 캐비닛을 생산 한 후에는 포장 및 배송이 필요합니다. 포장은 운송 중 섀시 및 캐비닛의 무결성과 안전성을 보호하는 것입니다. 제품의 모델과 크기에 따라 상자, 나무 상자, 플라스틱 필름 등과 같은 적절한 포장재를 선택할 수 있습니다. 배달 프로세스는 물류 채널 선택 및 핸드 오버 절차 처리와 같은 요소를 고려하여 제품을 제 시간에 안전하게 고객에게 전달할 수 있도록 고려해야합니다.
위의 것은 섀시 캐비닛의 제조 및 생산에서 몇 가지 주요 링크입니다. 각 링크는 상호 연결되어 없어야합니다. 이러한 링크의 효율적인 운영 및 협업은 섀시 및 캐비닛의 품질, 전달주기 및 고객 만족도를 결정합니다.
후 시간 : 10 월 10 일 -2023 년