In addition to using general sheet metal self-made parts, they are also equipped with profiles such as the mainstream 10% off profiles, 16% off profiles, and other profiles promoted by Rittal. Can be used to develop different products. Product materials are generally cold-rolled plates, hot-rolled plates, pre-galvanized plates, stainless steel plates and aluminum plates 5052. The product is roughly composed of base, frame, door panel, side panel and top cover. Figure 3: 10-fold profile and 16-fold profile.
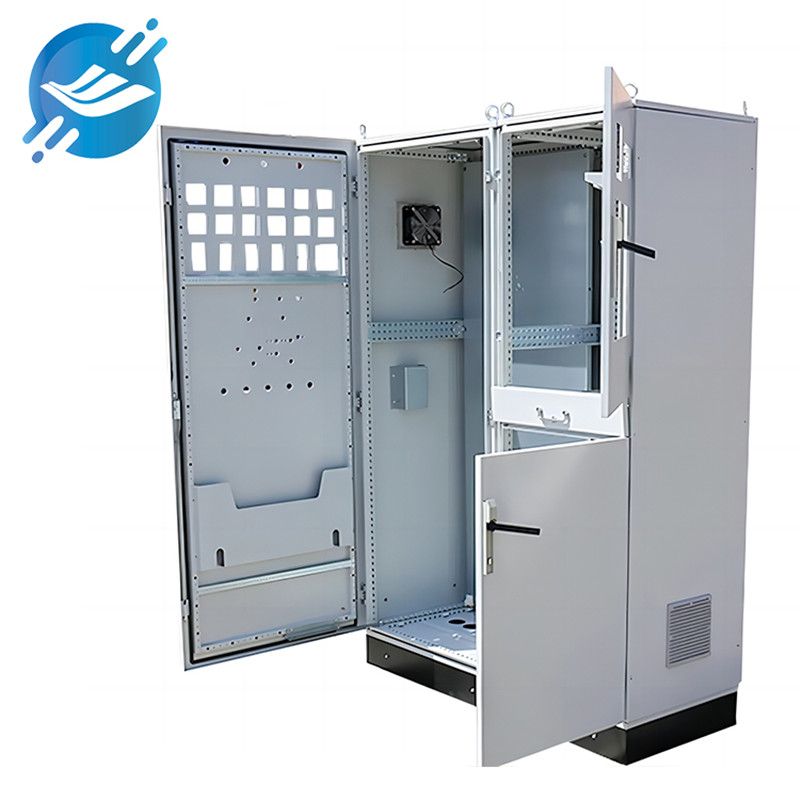
Sheet metal base:
The base is usually made of T2.5 or above plate bending or channel steel welding, and the surface treatment process uses hot-dip galvanizing or powder spraying. Figure 5 is an example of welding a certain base product sample. Base welding uses argon arc welding or carbon dioxide shielded welding depending on the product material; welding process parameters: welding machine current, voltage, wire material, diameter, wire feeding speed, welding method, direction and welding section length, etc.
Sheet metal frame:
The frame is usually made of T1.5 or above plates that are bent and spliced (riveted or screwed) or welded, and the surface treatment process is powder spraying or no treatment (except for cold-rolled steel plates). The design of the frame is generally assembly or welding; welding uses argon arc welding or carbon dioxide shielded welding depending on the product material; welding process parameters: welding machine current, voltage, wire material, diameter, wire feeding speed, welding method, direction, Welding section length, etc. Frame welding focuses on controlling diagonal tolerances and deformations, and its batch size requires higher reliability of pre-fabricated welding tooling.
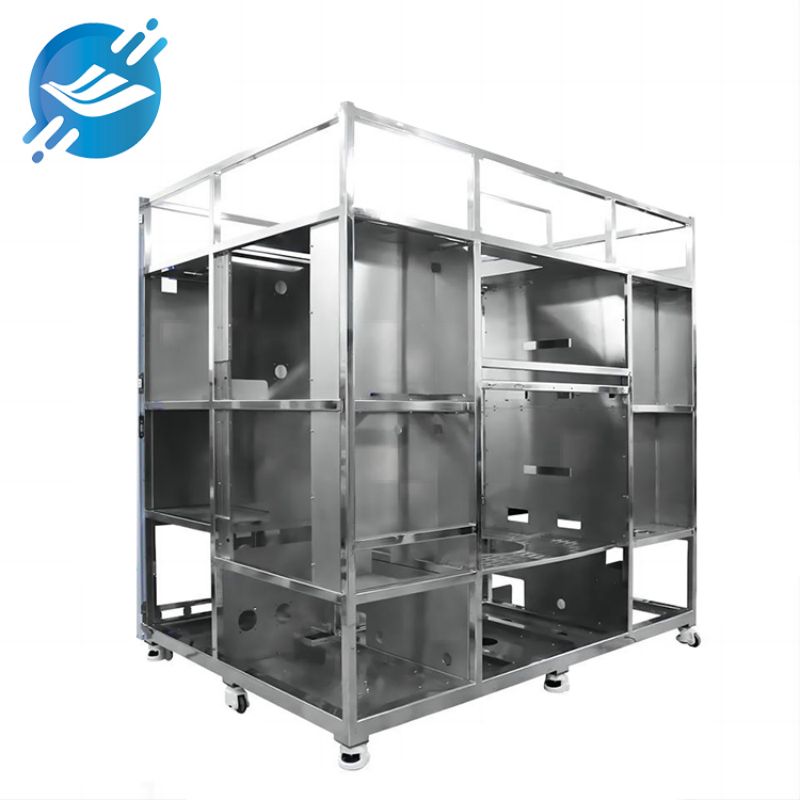
Sheet metal door panel:
Door panels are usually made of T1.2 or above plates by bending and welding (welding corners), and the surface treatment process is spray coating. Figure 7 shows a mesh door panel. Door panel welding uses argon arc welding, carbon dioxide shielded welding or flat plate butt welding depending on the product material; welding process parameters: welding machine current, voltage, welding wire material, diameter, wire feeding speed, welding method, direction and welding section length, etc. For mesh door panels, pay attention to controlling the welding stress and deformation during welding. Figure 7 Mesh door panel
Sheet metal top cover:
It is usually made of T1.0 or above plates by bending and welding (welding corners), and the surface treatment process is spray coating. The top cover is generally divided into indoor type and outdoor type; welding is based on different product materials, using argon arc welding or carbon dioxide shielded welding; welding process parameters: welding machine current, voltage, wire material, diameter, wire feeding speed, welding method, direction , welding section length, etc. Top cover welding focuses on controlling the impact of full welding of outdoor top covers on flatness and diagonal tolerances. Excellent tooling and fixture solutions will significantly improve welding quality and efficiency.
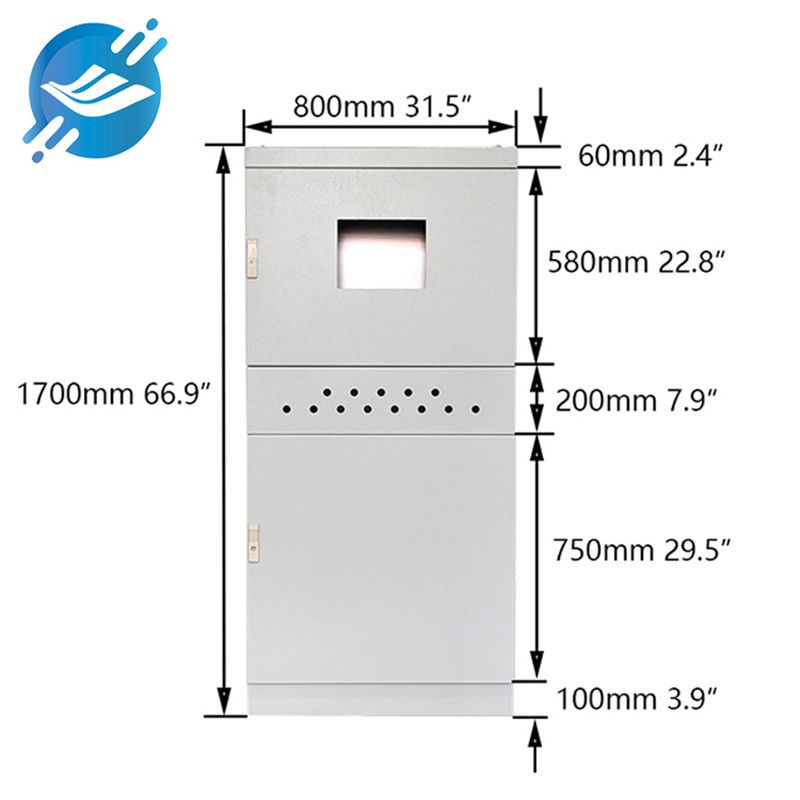
Sheet Metal Internal Mounting Parts:
Internal installation parts are usually divided into structural parts installation and component installation, which are required to be operated in strict accordance with the "XX Product Assembly/Electrical Installation Work Instructions". After the electrical installation is completed, various performance tests generally need to be completed.
Features and trends of sheet metal products:
Through the above component decomposition and module interpretation, it can be seen that sheet metal products have the following three characteristics:
⑴Profiling. It is conducive to the horizontal development of product platform design, and mass production helps to reduce costs.
⑵Modularization. According to the characteristics of each module, the flexible design can be purchased and assembled in modules, which helps to shorten the procurement cycle.
⑶Serialization. The platform products are developed according to different configuration requirements to meet the system requirements, forming a series of products, curing process, and mold-based production to improve production efficiency and shorten the supply cycle.
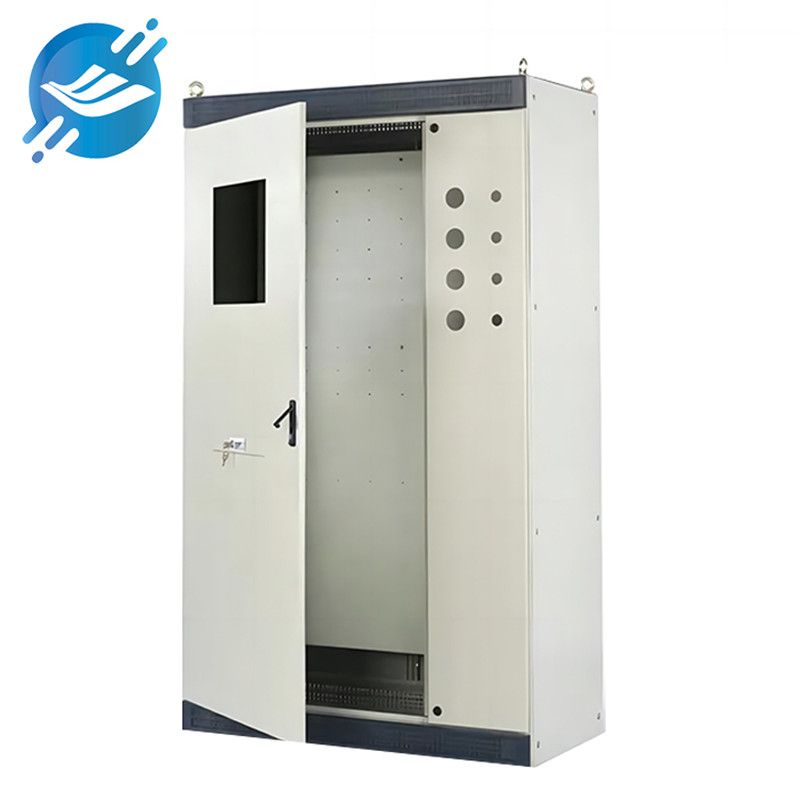
In short, the development of the low-voltage electrical appliance industry shows a stable development trend, and the sheet metal manufacturing suppliers that support the development of the low-voltage electrical appliance industry have more thoughts, starting from the design of new products and the development of new processes, and developing production automation. Improve the utilization rate of equipment and inventory turnover rate, and promote "lean production". With the new concept of "Industry 4.0", we will advance from manufacturing to "intelligent manufacturing" and make good use of network resources to go beyond sheet metal. The current situation of "meager profit" in production and processing has brought sheet metal production in low-voltage electrical appliances to a higher level. Facing opportunities and challenges, it is the general trend to provide customers with safer, smarter and greener electrical solutions.
Post time: Oct-31-2023