The cost of sheet metal processing parts mainly comes from three aspects: raw materials, stamping dies and human capital costs.
Among them, raw materials and stamping die costs account for the main proportion, and sheet metal manufacturing and processing plants need to start from these two aspects to reduce costs.
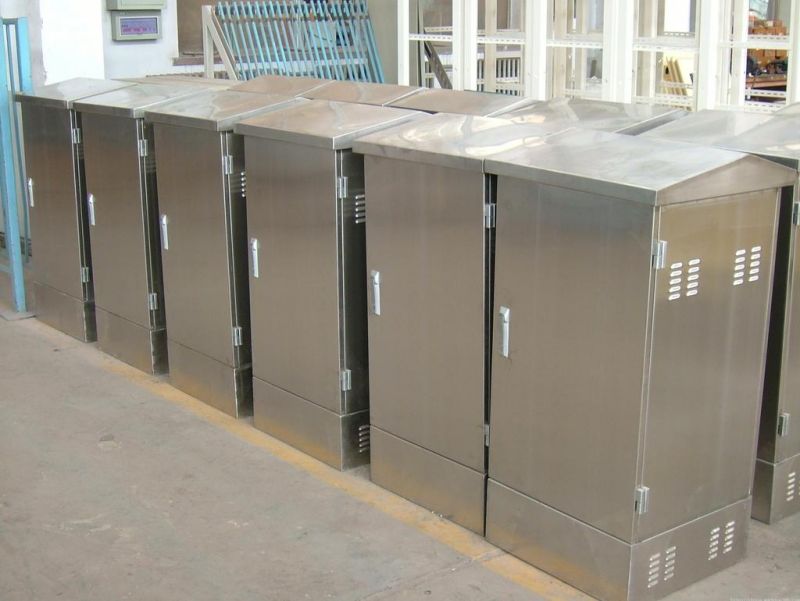
1. What the sheet metal parts look like
The shape of sheet metal parts should be conducive to layout, minimize waste, and improve raw material utilization. Effective sheet metal shape design can promote high utilization of raw materials and less waste during sheet metal layout, thereby reducing sheet metal raw material costs. Minor repair tips on the appearance design of sheet metal can greatly increase the utilization rate of raw materials, thereby saving the cost of parts.
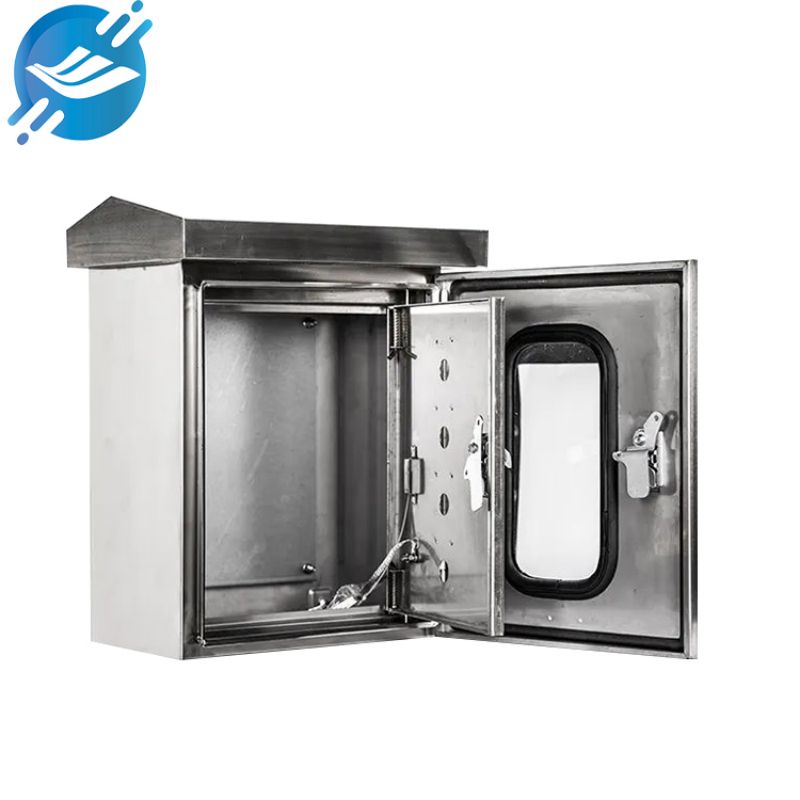
2. Reduce sheet metal size
Sheet metal size is one of the important factors that determine the cost of sheet metal stamping molds. The larger the sheet metal size, the larger the stamping mold specifications, and the higher the mold cost will be. This becomes more and more obvious when the stamping mold includes several sets of stamping process molds.
1) Avoid long and narrow features on sheet metal. Narrow and long sheet metal shapes not only have low hardness of the parts, but also consume heavy raw materials during sheet metal layout. At the same time, the long and narrow sheet metal features promote an increase in stamping die specifications and increase mold costs.
2) Prevent the sheet metal from having a "ten"-shaped appearance after completion. Sheet metal with a "ten"-shaped appearance design after completion will consume more raw materials during layout. At the same time, increase the specifications of the stamping mold and increase the cost of the mold. .
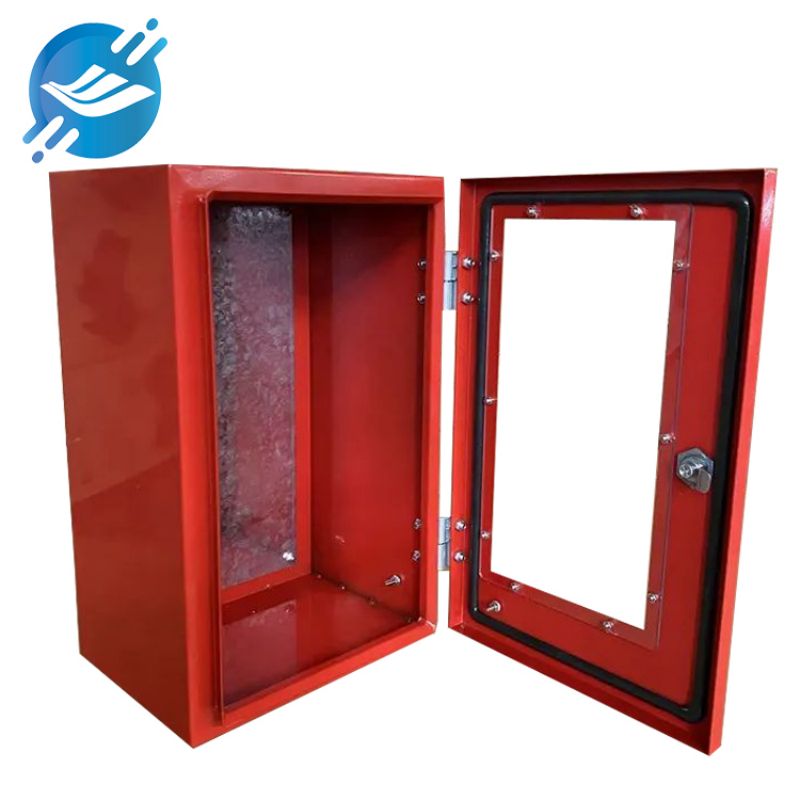
3. Make the sheet metal appearance design as simple as possible
Complex sheet metal appearance design requires complex concave molds and cavities, which increases mold production and processing costs. The appearance design of sheet metal should be as simple as possible.
4. Reduce the number of stamping die processes
There are two main types of stamping molds: engineering molds and continuous molds. A sheet metal project mold is likely to include several sets of process molds, such as chief molds, sheet metal bending molds, forming molds, and deburring molds. The greater the number of mold processes, the more processes there will be for the sheet metal mold, and the higher the cost of the stamping mold will be. The same is true for continuous modes. Mold cost is positively related to the number of mold processes. Therefore, in order to reduce the cost of stamping molds, the number of mold processes should be minimized.
a. Effectively define the adhesive edge of sheet metal bending. Unreasonable adhesive edges of sheet metal bending can easily slow down the sheet metal bending process.
b. Design products must minimize redundant sheet metal bending.
c. Design products must minimize folding and paving.
d. In addition, deburring generally requires a separate deburring process die.
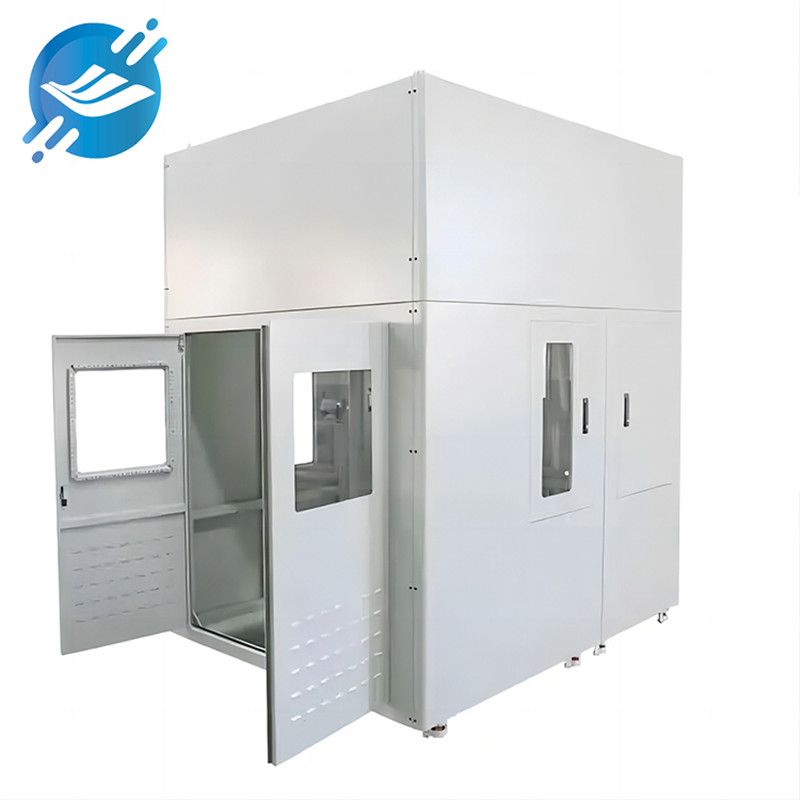
5. Effectively select the installation method of parts:
Locks ≤ rivets ≤ self-riveting ≤ welding ≤ ordinary screws ≤ hand-tightened screws
6. Reasonably arrange the sheet metal structure to reduce the total number of parts
Although the stamping manufacturing process does not allow sheet metal parts to have complex structures, within the scope that the sheet metal parts can be completed, the sheet metal parts structure should be reasonably arranged and the peripheral parts of the sheet metal parts should be combined to reduce the total number of parts and thereby reduce the product cost.
Post time: Oct-24-2023