The cost accounting of sheet metal parts is variable and depends on the specific drawings. It is not an immutable rule. You need to understand various sheet metal parts processing methods. Generally speaking, the price of the product = material fee + processing fee + (surface treatment fees) + various taxes + profits. If the sheet metal requires molds, mold fees will be added.
Mold fee (estimate the minimum number of stations required for molding based on the sheet metal manufacturing method, 1 station = 1 set of molds)
1. In the mold, different material surface treatments are selected according to the purpose of the mold: processing machine size, processing quantity, precision requirements, etc.;
2. Materials (according to the listed price, pay attention to whether it is a special steel type and whether it needs to be imported);
3. Freight (large sheet metal transportation costs);
4. Taxes;
5. 15~20% management and sales profit fee;
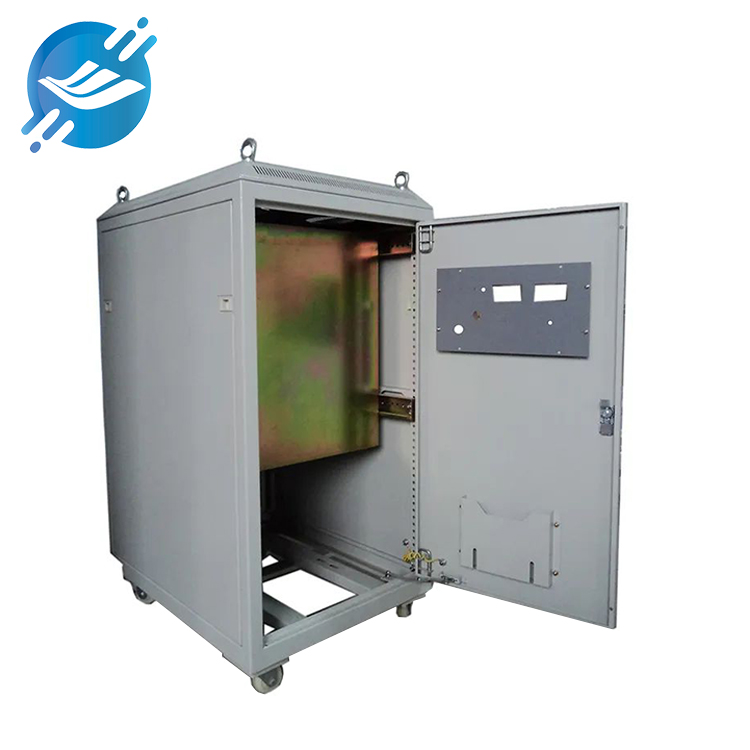
The total price of ordinary sheet metal parts processing is generally = material fee + processing fee + fixed standard parts + surface decoration + profit, management fee + tax rate.
When processing small batches without using molds, we generally calculate the net weight of the material * (1.2~1.3) = gross weight, and calculate the material cost based on the gross weight * unit price of the material; processing cost = (1~1.5) * material cost; decoration cost electroplating Generally, they are calculated based on the net weight of the parts. How much does one kilogram of parts cost? How much does one square meter of spraying cost? For example, nickel plating is calculated based on 8~10/kg, material fee + processing fee + fixed standard. Parts + surface decoration = cost, profit can generally be chosen as cost * (15%~20%); tax rate = (cost + profit, management fee) * 0.17. There is a note on this estimation: the material fee must not include tax.
When mass production requires the use of molds, the quotation is generally divided into mold quotations and parts quotations. If molds are used, the parts processing cost may be relatively low, and the total profit must be guaranteed by the production volume. The cost of raw materials in our factory is generally the net material minus the material utilization rate. Because there will be problems with leftover materials that cannot be used during the blanking process of sheet metal manufacturing. Some of them can be used now, but some can only be sold as scrap.
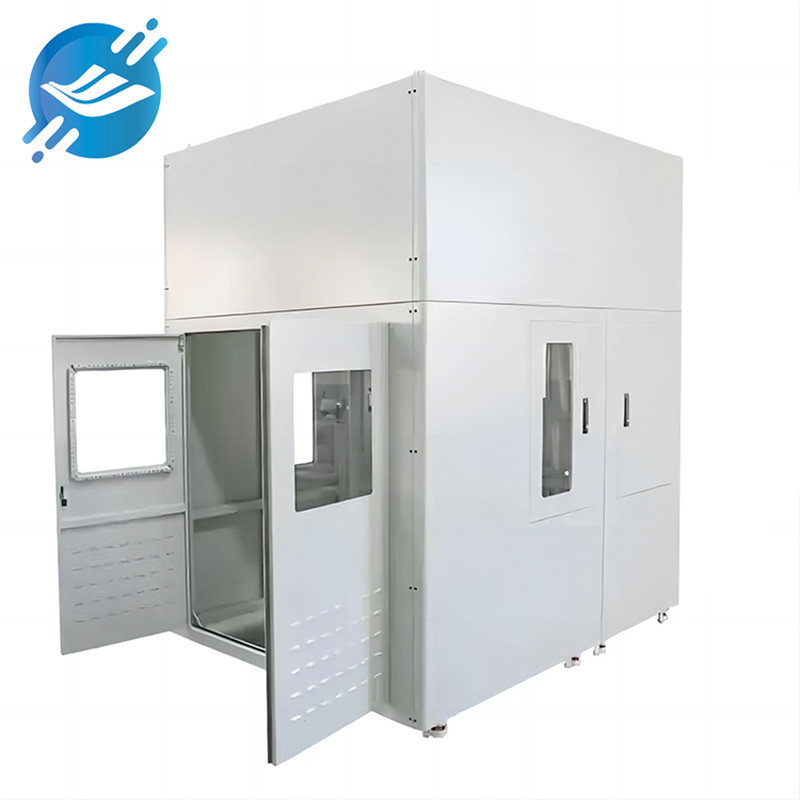
Sheet metal manufacturing The cost structure of metal parts is generally divided into the following parts:
1. Material cost
Material cost refers to the net material cost according to the drawing requirements = material volume * material density * material unit price.
2. Standard parts cost
Refers to the cost of standard parts required by the drawings.
3. Processing fees
Refers to the processing costs required for each process required to process the product. For details on the composition of each process, please refer to the "Cost Accounting Format" and "Cost Composition Table of Each Process". The main process cost components are now listed for explanation.
1) CNC blanking
Its cost composition = equipment depreciation and amortization + labor cost + auxiliary materials and equipment depreciation and amortization:
Equipment depreciation is calculated based on 5 years, and each year is recorded as 12 months, 22 days per month, and 8 hours per day.
For example: for 2 million yuan of equipment, equipment depreciation per hour = 200*10000/5/12/22/8=189.4 yuan/hour
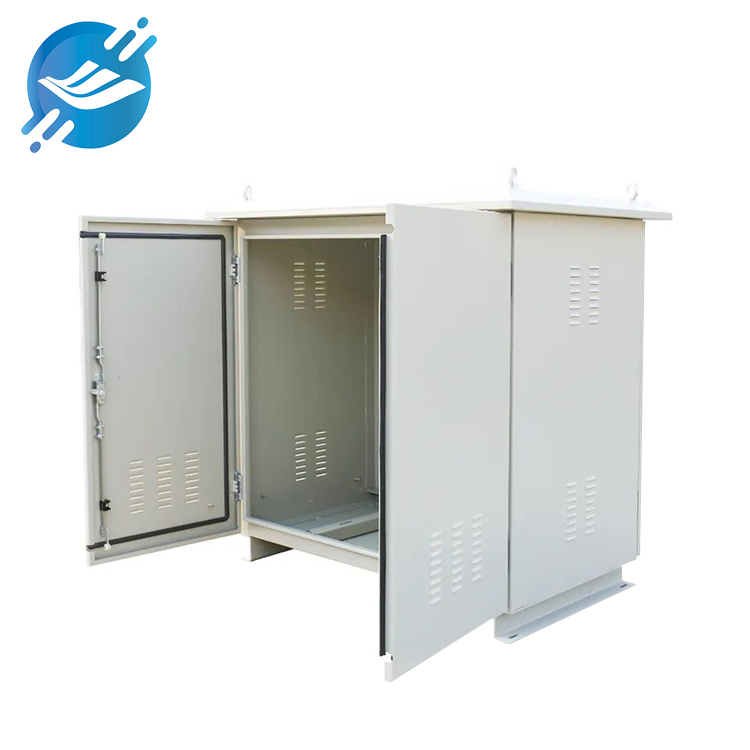
Labor cost:
Each CNC requires 3 technicians to operate. The average monthly salary of each technician is 1,800 yuan. They work 22 days a month, 8 hours a day, that is, the hourly cost = 1,800*3/22/8=31 yuan/hour. The cost of auxiliary materials: refers to The auxiliary production materials such as lubricants and volatile liquids required for equipment operation cost approximately 1,000 yuan per month for each piece of equipment. Based on 22 days per month and 8 hours per day, the hourly cost = 1,000/22/8 = 5.68 yuan/hour.
1) Bending
Its cost composition = equipment depreciation and amortization + labor cost + auxiliary materials and equipment depreciation and amortization:
Equipment depreciation is calculated based on 5 years, and each year is recorded as 12 months, 22 days per month, and 8 hours per day.
For example: for equipment worth RMB 500,000, equipment depreciation per minute = 50*10000/5/12/22/8/60=0.79 yuan/minute. It usually takes 10 seconds to 100 seconds to bend one bend, so the equipment depreciates per bending tool. =0.13-1.3 yuan/knife. Labor cost:
Each piece of equipment requires one technician to operate. The average monthly salary of each technician is 1,800 yuan. He works 22 days a month, 8 hours a day, that is, the cost per minute is 1,800/22/8/60=0.17 yuan/minute, and the average cost per minute is 1,800 yuan/month. It can make 1-2 bends, so: labor cost per bend = 0.08-0.17 yuan/knife cost of auxiliary materials:
The monthly cost of auxiliary materials for each bending machine is 600 yuan. Based on 22 days per month and 8 hours a day, the hourly cost = 600/22/8/60=0.06 yuan/knife
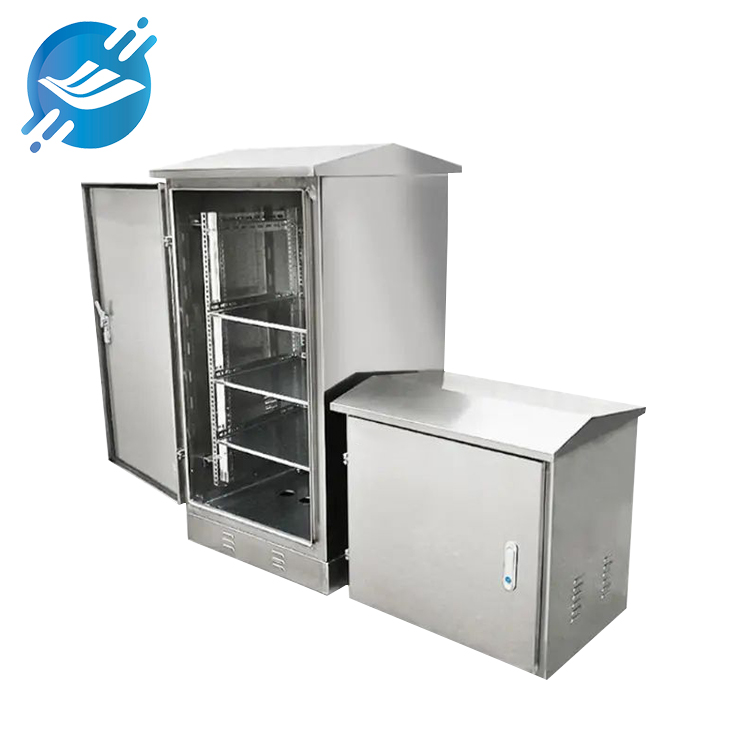
1) Surface treatment
Outsourced spraying costs are composed of the purchase price (such as electroplating, oxidation):
Spraying fee = powder material fee + labor fee + auxiliary material fee + equipment depreciation
Powder material fee: The calculation method is generally based on square meters. The price of each kilogram of powder ranges from 25-60 yuan (mainly related to customer requirements). Each kilogram of powder can generally spray 4-5 square meters. Powder material fee = 6-15 yuan/square meter
Labor cost: There are 15 people in the spraying line, each person is charged 1,200 yuan/month, 22 days a month, 8 hours a day, and can spray 30 square meters per hour. Labor cost=15*1200/22/8/30=3.4 yuan/square meter
Auxiliary material fee: mainly refers to the cost of the pre-treatment liquid and fuel used in the curing oven. It is 50,000 yuan per month. It is based on 22 days per month, 8 hours a day, and spraying 30 square meters per hour.
Auxiliary material fee = 9.47 yuan/square meter
Equipment depreciation: The investment in the spraying line is 1 million, and the depreciation is based on 5 years. It is December every year, 22 days a month, 8 hours a day, and sprays 30 square meters per hour. Equipment depreciation cost = 100*10000/5/12/22/8/30 = 3.16 yuan/square meter. Total spraying cost = 22-32 yuan/square meter. If partial protection spraying is required, the cost will be higher.
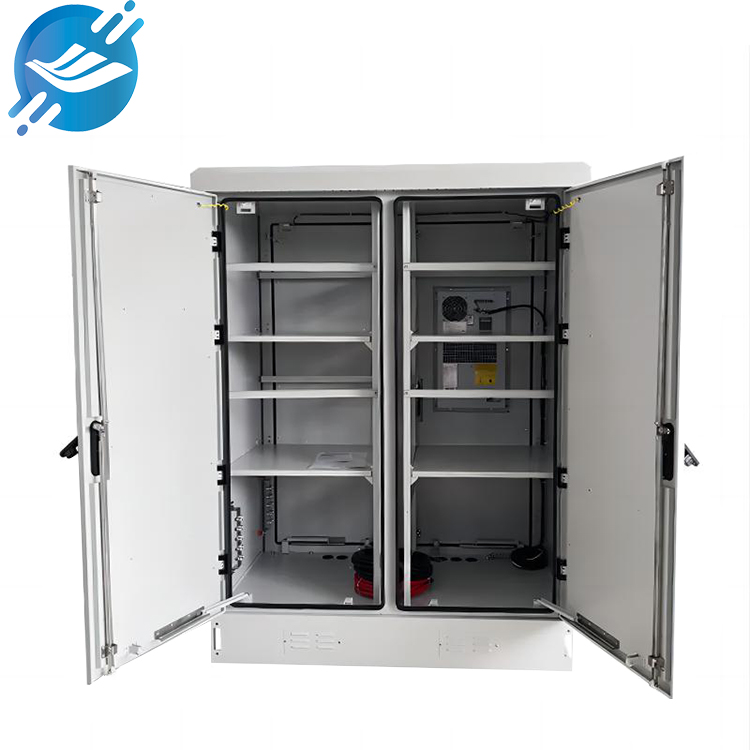
4. Packaging fee
Depending on the product, the packaging requirements are different and the price is different, generally 20-30 yuan/cubic meter.
5. Transportation management fees
Shipping costs are calculated into the product.
6. Management expenses
Management expenses have two parts: factory rent, water and electricity and financial expenses. Factory rent, water and electricity:
The monthly factory rent for water and electricity is 150,000 yuan, and the monthly output value is calculated as 4 million. The proportion of factory rent for water and electricity to the output value is =15/400=3.75%. Financial expenses:
Due to the mismatch between the receivable and payable cycles (we buy materials in cash and customers make monthly settlements within 60 days), we need to hold down funds for at least 3 months, and the bank interest rate is 1.25-1.5%.
Therefore: administrative expenses should account for about 5% of the total sales price.
7. Profit
Considering the company's long-term development and better customer service, our profit point is 10%-15%.
Post time: Nov-06-2023