When it comes to housing and protecting electrical components, the chassis cabinet plays a crucial role in ensuring the safety and functionality of the equipment. In the realm of high-voltage electrical systems, the need for a reliable and durable electrical cabinet is paramount. This is where the art of customizing aluminum high-voltage electrical cabinets comes into play, offering a tailored solution to meet specific requirements and standards.
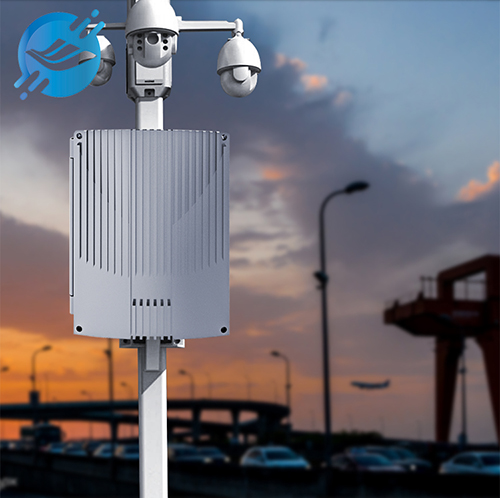
Understanding the Importance of Electrical Cabinet Customization
Electrical cabinets, especially those designed for high-voltage applications, require meticulous attention to detail and precision in their construction. The customization of these cabinets involves a comprehensive process that takes into account various factors such as the specific electrical components to be housed, environmental conditions, safety regulations, and space constraints. By customizing aluminum high-voltage electrical cabinets, manufacturers can ensure that the final product meets the exact needs of the application, providing optimal protection and performance.
The Role of Chassis Cabinet in Electrical Systems
The chassis cabinet, also known as the shell or housing, serves as the outer enclosure for electrical components. In the case of high-voltage systems, the chassis cabinet must be robust enough to withstand the rigors of the environment while providing adequate insulation and protection against electrical hazards. Aluminum, known for its lightweight yet durable properties, is a popular choice for constructing high-voltage electrical cabinets. Its corrosion resistance and thermal conductivity make it an ideal material for such applications.
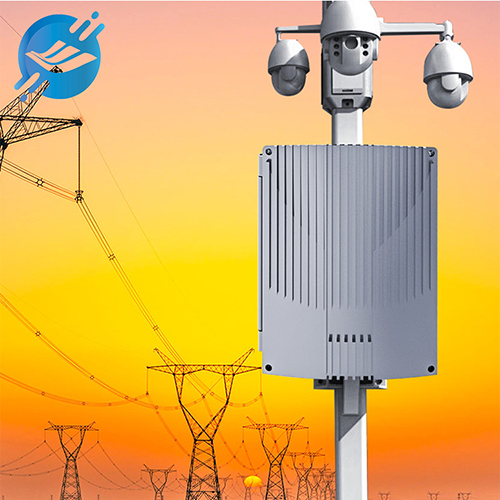
Shell Processing and Sheet Metal Shell Self-Manufacturing
The process of customizing aluminum high-voltage electrical cabinets involves shell processing, which encompasses the shaping, cutting, bending, and assembly of the aluminum sheets to form the cabinet's outer structure. Sheet metal shell self-manufacturing allows for greater flexibility in design and customization, as manufacturers can tailor the dimensions, features, and mounting options to suit the specific requirements of the electrical components and the installation environment.
Key Considerations for Electrical Cabinet Customization
When customizing aluminum high-voltage electrical cabinets, several key considerations come into play:
1. Environmental Factors: The cabinet must be designed to withstand the environmental conditions of its installation site, whether it be outdoor exposure to weather elements or indoor exposure to dust, moisture, or chemicals.
2. Thermal Management: High-voltage electrical components generate heat, requiring effective thermal management within the cabinet to prevent overheating and ensure optimal performance and longevity.
3. Safety Standards: Compliance with industry-specific safety standards and regulations is paramount to ensure the protection of personnel and equipment from electrical hazards.
4. Space Optimization: The cabinet design should maximize the use of available space while allowing for ease of access for maintenance and servicing of the enclosed electrical components.
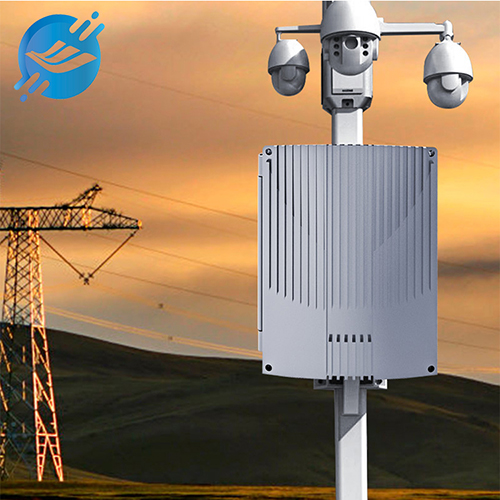
The Art of Customization: Tailoring Solutions for Unique Requirements
One of the primary advantages of customizing aluminum high-voltage electrical cabinets is the ability to tailor solutions for unique requirements. Whether it's accommodating non-standard component sizes, integrating specialized mounting options, or incorporating additional features such as ventilation, cable management, or access control, customization allows for a bespoke solution that aligns perfectly with the application's needs.
The Process of Customization: From Concept to Completion
The process of customizing aluminum high-voltage electrical cabinets typically involves the following stages:
1. Requirement Analysis: Understanding the specific requirements, constraints, and environmental factors that will influence the cabinet's design and functionality.
2. Design and Engineering: Collaborating with design and engineering teams to develop a customized cabinet solution that meets the identified requirements while adhering to industry standards and best practices.
3. Material Selection: Choosing the appropriate grade and thickness of aluminum, as well as any additional protective coatings or finishes, to ensure the cabinet's durability and longevity.
4. Fabrication and Assembly: Utilizing advanced manufacturing techniques such as CNC machining, laser cutting, and precision bending to fabricate the aluminum sheets into the desired cabinet structure, followed by meticulous assembly and welding processes.
5. Testing and Quality Assurance: Conducting rigorous testing to validate the cabinet's performance, including thermal analysis, electrical insulation testing, and environmental stress testing, to ensure its reliability in real-world conditions.
6. Installation and Support: Providing comprehensive installation support and documentation, as well as ongoing technical assistance to ensure the successful integration of the customized electrical cabinet into the overall system.
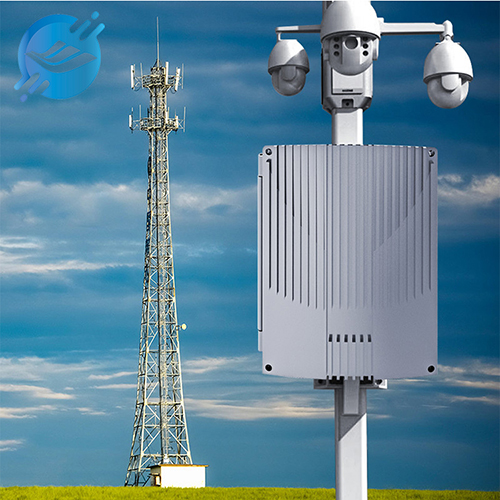
The Future of Electrical Cabinet Customization
As technology continues to evolve and the demand for high-voltage electrical systems grows, the need for customized aluminum electrical cabinets will only intensify. With advancements in materials, manufacturing processes, and design capabilities, the future of electrical cabinet customization holds the promise of even greater innovation and tailored solutions to meet the ever-changing needs of diverse industries and applications.
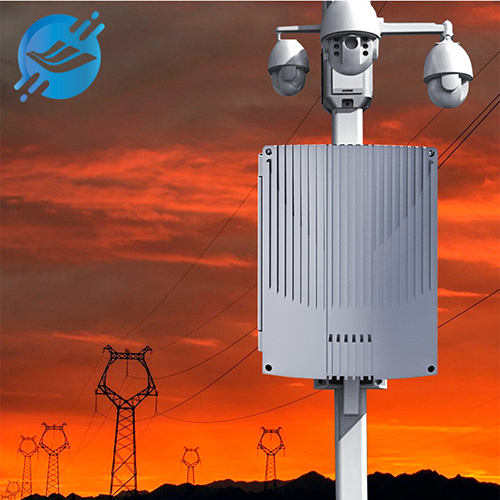
In conclusion, the art of customizing aluminum high-voltage electrical cabinets represents a harmonious blend of engineering expertise, precision manufacturing, and customer-centric solutions. By leveraging the capabilities of chassis cabinet customization, shell processing, and sheet metal shell self-manufacturing, manufacturers can deliver bespoke electrical cabinets that not only meet the stringent requirements of high-voltage applications but also pave the way for enhanced safety, reliability, and performance in the electrified world of tomorrow.
Post time: Sep-02-2024